Fused Silica Powder: Guide to Properties & Applications
2024.07.01admin
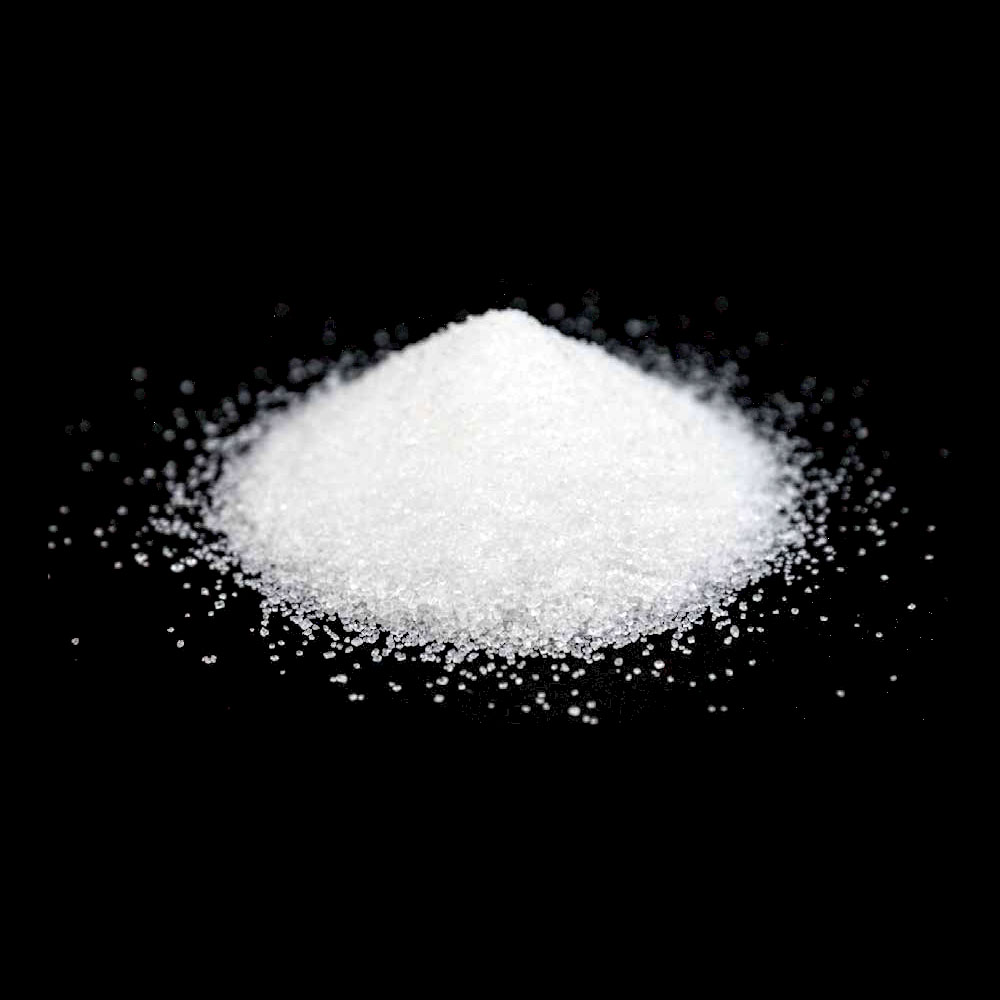
A Comprehensive Guide to Fused Silica Powder
Fused silica powder also commonly known as fused quartz powder or quartz flour is a very versatile material and is used extensively in numerous industrial and scientific applications. These excellent characteristics that including high chemical resistance, low coefficient of thermal expansion, and high purity make this powder versatile. If you are looking for a material that can withstand heat, maintain its dimensions, and above all, offer the highest levels of purity then it could be the solution that you are looking for.
Understanding Fused Silica Powder:
High-quality silica sand is the raw material used to make fused silica powder by fusing it at about 1700°C and it is simply silicon dioxide (SiO₂). The powder is then quickly quenched. This method gives a product in the form of a glassy substance that has a particular structure on the microscopic level that endows it with peculiar characteristics.
Key Properties of Fused Silica Powder
Fused quartz powder commonly known as fused silica powder is the most efficient and chemically pure material. Owing to these characteristics, this material has found a lot of use in various commercial and scientific purposes. Let’s examine the salient features of fused silica powder that set it apart from the competition:
- Unmatched Purity:
Silica powder is one of the most chemically pure materials that can be bought in the market with SiO₂ content greater than 99. 9%. This very high purity minimizes the chance of contamination and ensures high performance in various applications.
- Dimensional Stability Under Pressure:
It has one of the lowest coefficients of thermal expansion, for example, numerous other substances change their shape when subjected to temperature variations. Since the dimensional changes are at their minimum, it is best for uses where the shape and size have to be precise.
- Chemical Invincibility:
The excellent chemical inertness of fused silica powder to a wide variety of chemicals including organic solvents, acids, and alkalis is shown. Due to its excellent durability, it can grow in harsh conditions without becoming damaged, which makes it a useful choice for many applications.
- Thermal Shock Champion:
There are some materials that get severely affected if there is a sudden change in temperature. While it does not tend to break or crack in the event of sudden changes in temperature because it has a low coefficient of thermal expansion. Due to its toughness, it is suitable for thermal cycling procedures.
- Optical Clarity (for Particular Grades):
Some of the fused silica powder is optically pure. Owing to the fact that they are highly transparent, their use can be readily made in lens systems, prism systems, and other multi-element optical systems that are found in scientific instruments and lasers.
Manufacturing Process for Fused Silica Powder
Due to the mentioned characteristics, fused silica powder is widely used in various industries. Nevertheless, how is this substance so dramatically produced? Below are the main processes through which ordinary silica sand is processed into superior silica powder.
The Predominant Force in Electrofusion:
The common method of producing fused silica powder is through electrofusion. This procedure entails using electricity’s inherent power:
- High-Purity Start:
The process first calls for the use of high-purity silica sand which has been specifically chosen for the task. This choice ensures the end product is a very pure powder and there is no presence of other impurities.
- Molten Majesty:
Once it is selected, the silica sand has to be heated to temperatures of above 1700oC in an electric arc furnace. The sand is hence heated to the extent that it liquefies into silica.
- Quick Quench:
The molten silica does not have time to solidify even for a second. This is followed by quenching with air or water to give a glassy frit. This rapid cooling process is vital in the development of the trademark amorphous structure of the fused silica.
- Grinding to Perfection:
Then the glassy frit is crushed and milled to a fine powder. Grinding can be done to produce particles of various sizes depending on the intended use.
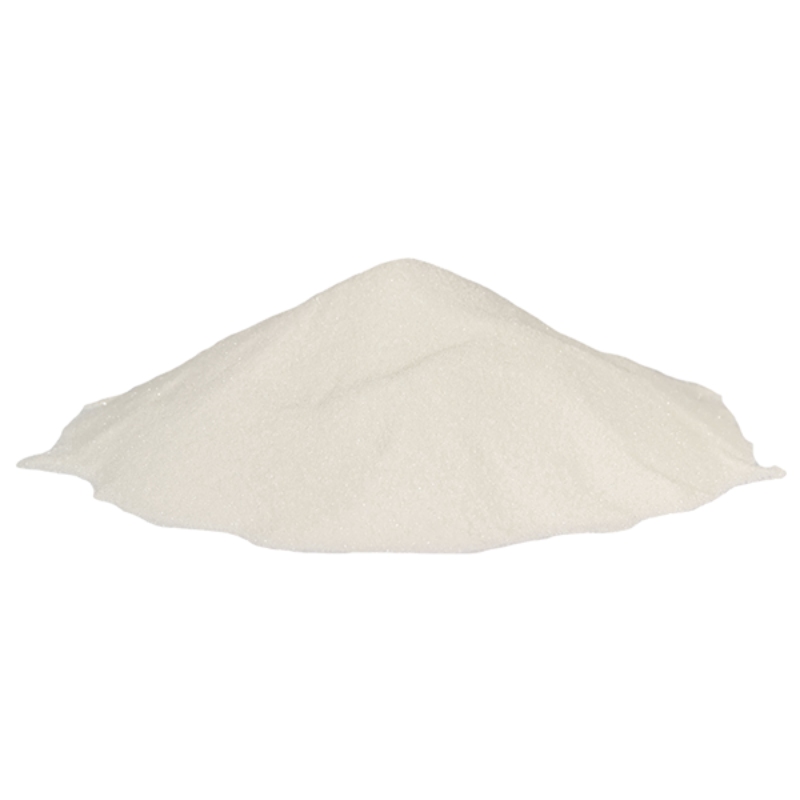
Beyond Electrofusion: Other Approaches
Although electrofusion is the most common process, there are other ways as well, each with advantages of its own, to produce fused silica powder:
- Chemical Vapor Deposition (CVD):
This process results to the production of fused silica powder through the deposition of silicon dioxide vapor on a heated surface. Both particle size and the impurity level of the CVD process can be very accurately controlled.
- Flame Hydrolysis:
Here, the silicon tetrachloride (SiCl₄) is converted into fused silica particles by burning the same. This is a cheaper method of producing fused silica powder especially in the coarser forms.
Selecting the Appropriate Approach:
This is because while choosing the production process, factors such as particle size distribution, cost and purity level have to be taken into consideration. With the knowledge of these techniques, manufacturers can at least know how to choose the most appropriate one depending on the situation.
Applications of Fused Silica Powder:
Given that it has so many unique properties, it is not just a substance that can be used in many fields but it is a compulsory element for success in numerous industries. Let’s look at a few of the more intriguing uses for fused silica powder:
Investing in Casting: An exact match means:
One of the most important elements of the investment casting mould is sprue and it is used throughout the process. This is the reason why:
- Purity Pays Off:
Such high purity of the powder minimizes the possibility of contamination, thus, contributing to the production of castings with smooth surface finishes.
- Dimensional Stability Is Everything:
The thermal expansion coefficient of this powder is very low, and this means that the mould will not deform during the casting process, thus delivering the right results.
- The main focus is on thermal shock resistance:
It is ideal for thermal cycling which is required in investment casting as it has the ability to handle sudden changes in temperature.
Advantages
This Article also shows that the application of silica powder is not only limited to investment casting. Here are a few more uses for it:
- Refractory Reinforcement:
Due to its high melting point thermal stability and chemical resistance, it is used in refractory materials for furnaces and kilns.
- Dental Strength and Aesthetics:
Fused silica powder is one of the components of dental porcelains and some composites that enhance the biocompatibility, mechanical properties, and appearance of dental materials.
- Electronic Reliability:
High-purity fused silica powder, which has excellent electrical insulation characteristics and excellent stability of size, is widely used in the production of electronics parts including substrates and insulators.
Benefits of Using Fused Silica Powder:
This is not only a substance, but a valuable asset with a long list of benefits for scientific and industrial applications. Now let’s examine the main benefits that set fused silica powder apart:
- Purity Powerhouse:
It is the most chemically inert of them all with a silicon dioxide content of about 99. 9%. This incredible feature enhances the prevention of contamination hence assuring efficiency and high results in numerous uses.
- Dimensional Stability You Can Rely On:
Fused silica powder is characterized by a low coefficient of thermal expansion; thus it does not deform at different temperatures. Due to the amount of dimensional changes that are minimal, it is suitable for use in places that require high precision of shape and size. More accuracy decreases the need for the rework and, consequently, leads to a lower cost.
- A Protective Barrier Against Degradation:
Fused silica powder has also a very good chemical resistance meaning that it is not easily and quickly affected by a wide range of chemicals like acids, alkalis, and organic solvents. Because of this it is possible for the equipment to endure tough conditions and not get damaged, thus requiring minimal maintenance and can be used for a long period of time.
Manufacturer of Thermal Shock: The Result of “Heat” Handling
It should be noted that sharp changes in temperature are often dangerous for many materials. But fused silica powder cannot break or crack easily even under the condition of temperature fluctuations because its thermal expansion is low. This makes it suitable for use in thermal cycling operations which help in minimizing on time that is not in use and hence increases the overall efficiency of the system.
- Unrestricted Versatility:
Fused silica powder has several advantages due to its properties. It can be employed in several applications since they are available in various size and level of purity. This allows the manufacturers to determine the exact characteristics of the material for the best outcome.
Fused Silica Powder: It is very Effective, Yet One Should Not Overlook the Following Factors.
Silica powder is therefore a great material to work with but like any other material, there are certain factors that must be put into consideration to ensure that one gets the best results. When using this adaptable powder in your projects, bear the following in mind:
- Cost factor:
Compared to some of the substitute materials, high-purity fused silica powder may be expensive. Consider your demands purposely and compare it with the benefits it offers for your specific application with the price.
- Brutality Take Note:
It is recommended that powdered fused silica may be abrasive. For personnel safety and to prevent damage of machinery during handling, the right equipment and method of handling is necessary.
- Moisture Matters:
Hygroscopic silica powders are those that have the ability to absorb moisture from the surrounding environment. This moisture absorption, however, may cause some effect on the output. Avoid moisture damage by using proper handling procedures and proper storage methods.
Conclusion:
KAMROLLER is a well-known fusion silica powder supplier that boasts an exceptionally high purity and consistent quality of the product. The use of advanced production methods and strict quality control measures ensures that you will receive the fused silica powder that meets the desired characteristics of your application.
Read more: Fused SiO2 Powder: Properties & Applications