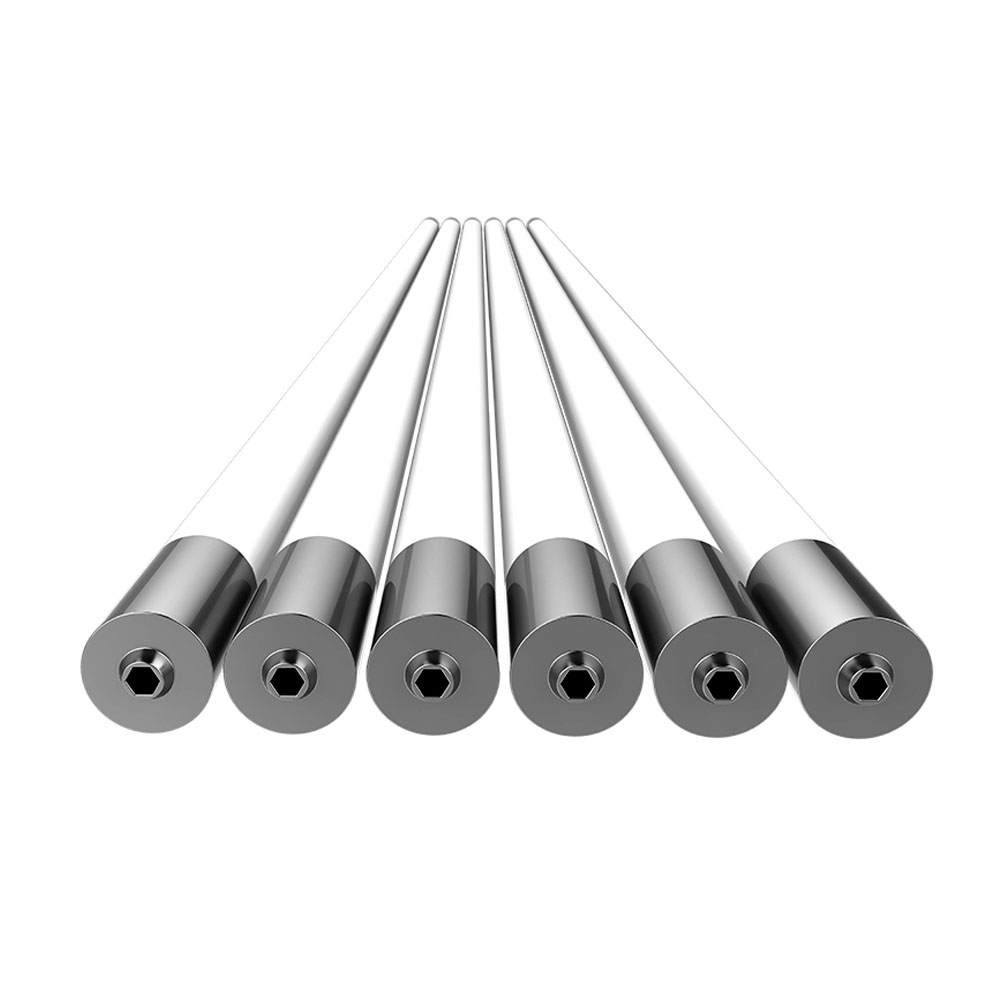
Fused Silica Roller For Automotive Parts Annealing Furnace
✦ High temperature resistance: – Fused quartz rollers made of high-purity fused silica material have excellent high temperature resistance. They can withstand temperatures up to 1500°C and show excellent stability and durability when used in automotive parts annealing furnaces.
✦ Excellent thermal conductivity: Fused quartz rollers have excellent thermal conductivity and can conduct heat quickly and evenly. This property helps maintain a consistent temperature of automotive parts during the annealing process, thereby improving product quality and process efficiency.
✦ Chemical Stability:- Fused quartz rollers have excellent chemical stability and are resistant to attack and corrosion by a wide range of chemicals.- This makes it ideal for use in the annealing process of automotive parts due to its ability to maintain stability in high temperature and chemical environments.
✦ Strong customizability: – According to different needs and applications, fused quartz rollers can be customized – including the customization of roller diameter, length, shape and other parameters to meet the specific requirements of different customers.
Product Image
Product Certificate
-
DESCRIPTION
-
SPECIFICATION
-
FQA
Introducing our Fused Silica Roller for Automotive Parts Annealing Furnaces, a top-tier solution designed to withstand extreme temperatures. Precisely manufactured using high-quality fused silica ceramic materials, this roller ensures exceptional thermal stability, durability, and reliability. Its superior performance makes it the perfect choice for automotive manufacturing facilities seeking dependable and efficient annealing processes.Its exceptional performance makes it the ideal choice for automotive manufacturing facilities looking for reliable and efficient annealing processes.
Invest in Kamroller’s Fused Silica Roller for Automotive Parts Annealing Furnace and experience the difference that precision engineering can make in your automotive manufacturing processes. With superior thermal stability, uniform heat distribution, and customizable designs, these rollers ensure optimal annealing results and enhance the quality and performance of automotive components.
Applications of Fused Silica Roller for Automotive Parts Annealing Furnace
The Fused Silica Roller finds widespread application in automotive manufacturing, particularly in the production of critical components requiring precise heat treatment, such as:
Engine Parts: Including cylinder heads, pistons, and crankshafts, where precise control over mechanical properties is essential for optimal engine performance and durability.
Transmission Components: Such as gears, shafts, and housings, where uniform heat treatment ensures proper hardness and wear resistance to withstand the demands of automotive transmission systems.
Suspension and Chassis Parts: Including springs, control arms, and subframes, where controlled cooling rates during annealing prevent distortion and maintain dimensional accuracy for proper vehicle handling and safety.
Why Trust Kamroller
Kamroller has established itself as a trusted provider of high-performance rollers for industrial applications, with a commitment to quality, innovation, and customer satisfaction. Here’s why you can trust Kamroller for your automotive parts annealing furnace needs:
Expertise and Experience: With years of experience in precision engineering, Kamroller has the knowledge and expertise to deliver superior rollers tailored to meet the unique requirements of automotive manufacturing processes.
Гарантія якості: Each Fused Silica Roller undergoes rigorous quality control checks to ensure thermal stability, dimensional accuracy, and reliability, meeting the highest industry standards for automotive parts production.
Global Reputation: Trusted by leading automotive manufacturers worldwide, Kamroller is known for its reliability, performance, and commitment to excellence in providing rollers for automotive parts annealing furnaces.
High-quality fused silica rollers offer numerous advantages, including superior thermal shock resistance, high temperature stability, and excellent chemical inertness. These rollers ensure efficient heat transfer and minimal thermal expansion, making them ideal for high-temperature applications such as glass tempering, annealing, and metal processing. Additionally, they provide long service life and consistent performance, reducing maintenance costs and downtime. Reputable manufacturers and suppliers offer certification and quality assurance, ensuring that their products meet stringent industry standards. Choosing certified suppliers guarantees reliability and optimal performance in demanding industrial environments
What is a Fused Silica Roller?
A fused silica roller is a type of high-temperature-resistant roller made from fused silica (silicon dioxide in a non-crystalline form). These rollers are specifically designed to withstand extreme temperatures and thermal shock, making them ideal for use in various high-temperature industrial applications, such as annealing furnaces in the automotive industry.
What are the Benefits of Using Fused Silica Rollers in Annealing Furnaces?
High Thermal Stability: Fused silica rollers can withstand high temperatures without deformation or damage, ensuring consistent performance in the annealing process. Low Thermal Expansion: They have a very low coefficient of thermal expansion, reducing the risk of thermal stress and cracking. High Purity: Made from high-purity silica, these rollers have excellent chemical resistance, preventing contamination of automotive parts during the annealing process. Довговічність: Fused silica rollers are resistant to wear and thermal shock, providing a long service life and reducing maintenance costs.
How Do Fused Silica Rollers Enhance the Annealing Process?
Fused silica rollers provide a stable and uniform platform for automotive parts during the annealing process, ensuring even heating and cooling. This uniformity helps in reducing internal stresses and improving the mechanical properties of the automotive parts, leading to better performance and longevity.
What Applications in the Automotive Industry Use Fused Silica Rollers?
Fused silica rollers are primarily used in the annealing furnaces where automotive parts such as engine components, transmission parts, and structural elements are heat-treated to improve their strength and durability. They are also used in other high-temperature processes like coating, tempering, and glazing.
What are the Key Specifications to Consider When Selecting Fused Silica Rollers?
Roller Diameter and Length: Ensure they match the requirements of the annealing furnace. Maximum Operating Temperature: Should be suitable for the specific heat treatment process. Thermal Conductivity: Low thermal conductivity is preferred to prevent heat loss and ensure energy efficiency. Surface Finish: Smooth surface finish to prevent damage to automotive parts.
How Should Fused Silica Rollers be Maintained?
Regular Inspection: Periodically inspect for cracks, wear, and other signs of damage. Cleaning: Keep the rollers clean from any debris or contaminants to ensure smooth operation. Proper Handling: Handle with care to avoid impacts and thermal shocks that can cause damage.
Can Fused Silica Rollers be Customized?
Yes, fused silica rollers can often be customized to meet specific requirements regarding size, shape, and performance characteristics. Customization ensures optimal integration with the annealing furnace and the specific needs of the automotive parts being treated.
Where Can I Source High-Quality Fused Silica Rollers?
High-quality fused silica rollers can be sourced from specialized manufacturers and suppliers of industrial furnace components. It's essential to choose reputable suppliers who can provide certification and quality assurance for their products.