Fused Silica Roller: Guide to Properties, Applications & Benefits
2024.06.30admin
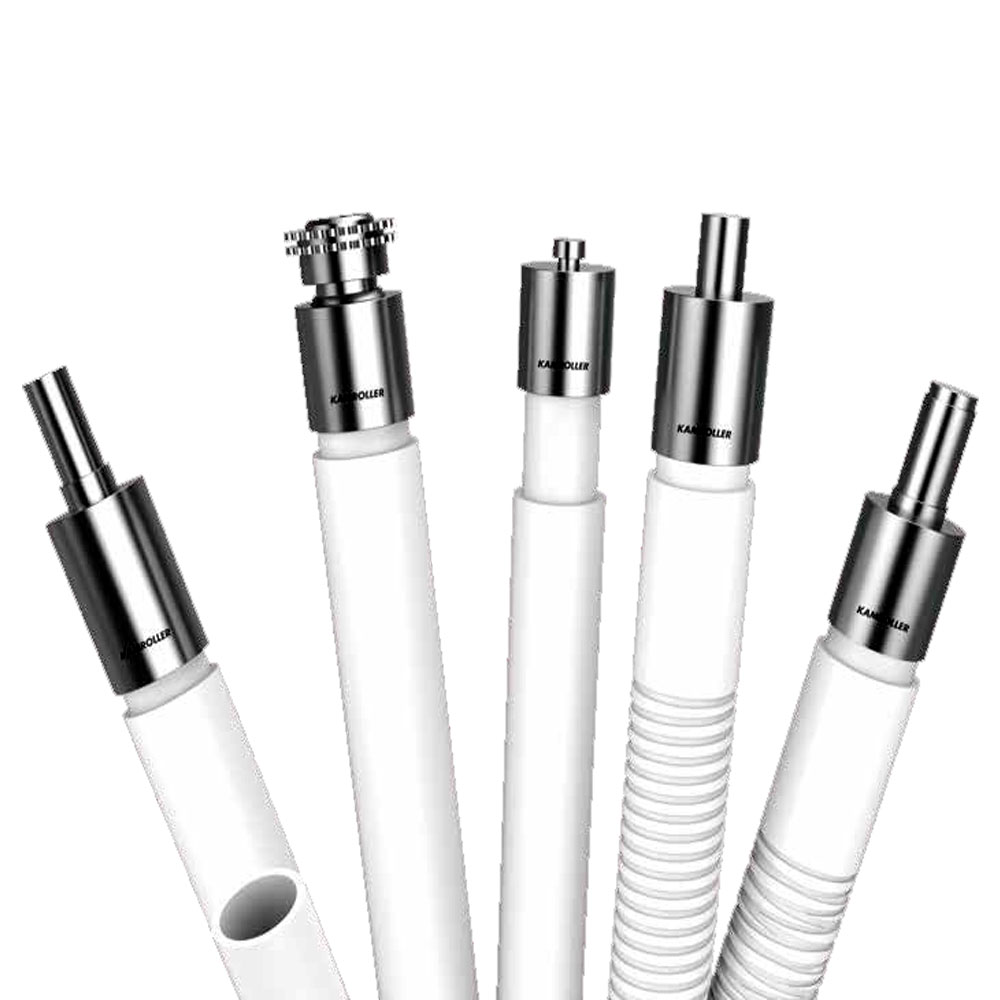
Fused Silica Rollers Overview
A fused silica roller is the most suitable for industrial applications that need high temperature, and precise and consistent performance. These are very special rollers that are produced from high-purity silicon dioxide (SiO₂) and have some incredible properties that make them suitable for use in many fields. Fused silica rollers have many advantages for use in the manipulation of the demanding environment of glass manufacturing or the assurance of stability in high-temperature furnaces.
Fused silica rollers have the following properties
It can be said that silica rollers’ excellent performance is due to certain properties of the material that is used in their construction.
- မြင့်မားသောသန့်ရှင်းမှု:
The silicon dioxide content of the present compound is above 99. Thus, the use of silica rollers decreases the likelihood of contamination and ensures proper functioning in various tasks, in 9% of cases.
- Ultra-Low Thermal Expansion:
They possess a very low coefficient of thermal expansion, whereas materials change shape when the temperature is altered. Due to the minimal alteration in the dimensions, they are suitable where there is a need to have strict control over the size and shape.
- Outstanding Thermal Stability:
These are fusible rollers that have melting points which are higher than 1600 degrees centigrade, this shows that they are very hot to handle. These are because of their high-temperature stability and hence they can work efficiently in extreme conditions.
- Excellent Chemical Resistance:
When it comes to exposure to a number of chemicals including acids, alkalis, and organic solvents, silica rollers are highly resistant. Due to this resistance, they are able to exist in conditions that are unfriendly chemically.
- Superior Surface Finish:
When the fused silica rollers are being made, it is possible to obtain very smooth surfaces for the rollers as they are worn down less easily and do not produce much friction when in use.
Fused Silica Rollers များ: Generating Power for Industries
Silica rollers which are made from high purity silicon dioxide are not just rollers but the foundation of many industrial systems. These have high resistance to high temperatures, very low coefficient of thermal expansion, and high chemical resistance and are thus suitable for various uses. Let’s take a tour of some of the major sectors where these rollers are the best:
- Semiconductor Marvels:
This is an area of semiconductors and thus the field is still evolving. This is where the high purity of the fused silica rollers as well as their very low coefficient of thermal expansion can be Put to use. These characteristics ensure that there is accurate dimension control during the lithography process which plays a very crucial role in the creation of intricate circuits on the silicon wafer.
- Optical Applications:
A definite positive aspect of Fused silica rollers in some grades is characterized by very high UV transmittance. Due to this property, they are very suitable for many optical uses such as windows and lenses in scientific equipment and in UV curing processes where the amount of UV light that is let in has to be well controlled.
- Heroes of the High-Temperature Furnace:
For instance, in applications where heat is a factor, fused silica rollers never fail to deliver. They can withstand very high temperatures; in many cases, even in excess of 1600 degrees centigrade, without bending or breaking due to their high thermal stability. This therefore allows furnaces to treat the materials and spread heat uniformly across the entire materials being treated.
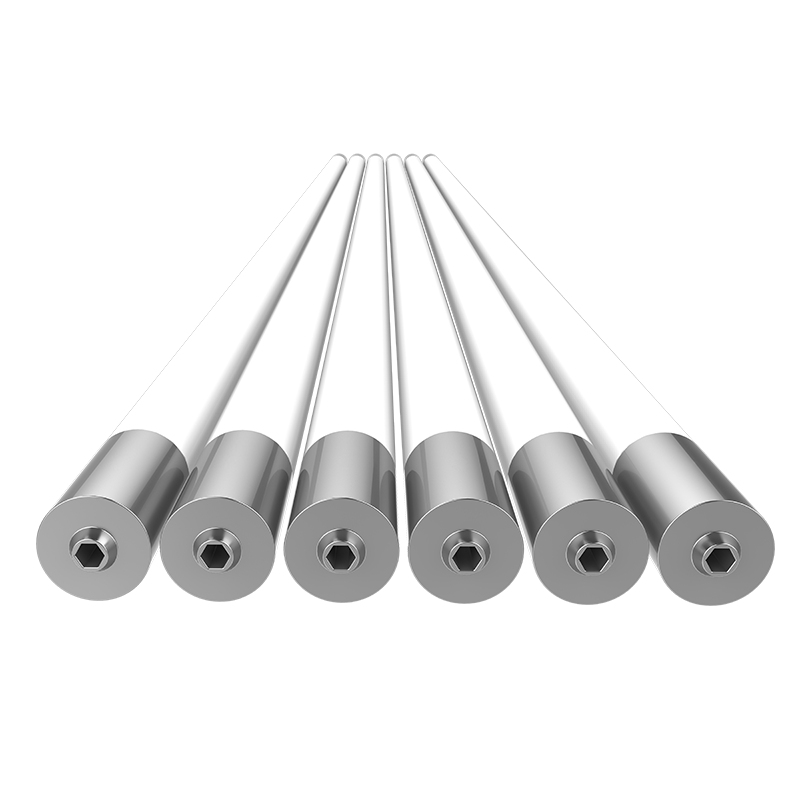
Benefits of Fused Silica Rollers
The fused silica roller is an enhancement of performance and at the same time is an industrial workhorse. It stems from their special material qualities that make them offer a number of benefits to enhance a number of industrial productions. Let us examine the strong arguments supporting the viability of fused silica rollers:
- Precision Powerhouse:
The thermal coefficient of expansion of silica rollers is very low thus minimizing the effects of thermal expansion. This results in unswerving accuracy which ensures repetitive results in uses like semiconductor lithography and glass heat treatment.
- Durability Dynasty:
In terms of the service lifespan, fused silica roller has no equal. They are also characterized by high resistance to temperatures, chemicals, and mechanical stresses, and that is why they have a long and reliable service life. This reduces the rate of replacements in the long run and, therefore, can be very economical.
- Demolition Crew Downtime:
The strength of the fused rollers is that it minimizes the time spent on maintenance and replacement. They increase manufacturing productivity by ensuring that your operations continue to roll without interruption owing to their excellent wear and tear and dimensional stability.
- Champion of Quality:
These rollers’ characteristics help to support the consistent production of high-quality products, which is the main goal. These rollers offer you ways of achieving excellent results ranging from ensuring that the right dimensions are maintained in semiconductors to the right thickness of the glass.
- Versatility Vanguard:
They are a flexible type of champion as opposed to a one-dimensional choice. It efficiently fulfills the specific functionalities of numerous applications and is offered in different dimensions as well as surface finishes. Due to this factor, you are in a position to identify the suitable fused silica roller for your specific needs.
Fused Silica Rollers များ: Why do you need to buy them?
Due to these exceptional characteristics, silica rollers are considered industrial behemoths. As with any other powerful instrument, however, it is necessary to understand what factors one should consider to get the most out of it. The following guide will help you negotiate these factors and make sure you make the most of fused silica rollers:
- Cost factor:
Some of the substitute materials for high-purity silica rollers may be cheaper in the market even if they are not as effective. Ensure that you look at the requirements that your application has and the future benefits that come with it such as less downtime and high-quality work as opposed to the costs involved.
- Abrasiveness Be Aware:
Fused silica powder, the predecessor of silica rollers is abrasive; therefore, one should be careful. Even if the rollers themselves are not as sharp, safe handling of workers and avoiding strains on machinery means proper tools and techniques are to be used. Also depending on the application that you intend to use the saw for you may require dust collection systems.
- Thermal Shock Susceptibility:
To some extent silica rollers are quite thermally shock resistant; nonetheless, rapid and highly extreme variations in temperature are not recommended. It is vital to adhere to proper heating and cooling measures in order to avoid cracks or fractures. It is advisable to consult with your fused silica roller supplier on appropriate heating and cooling rates that ought to be followed.
- Moisture Matters (for Certain classes):
Hygroscopic or those that are able to absorb moisture from the surrounding air are some of the types of silica rollers. This moisture absorption makes the performance in sensitive applications to be affected in some way. When working with grades that are likely to be affected by moisture, ensure that you store items in low-humidity conditions, and when dealing with the materials ensure that you do not expose them to moisture.
Fused Silica Rollers Has a Brighter Future
Therefore, fused silica roller has become popular in different fields due to its excellent characteristics. Yet there is more to the story. An even brighter future for these amazing rollers is guaranteed by the material science community’s nerve to innovate. Let’s investigate the fascinating developments that lie ahead:
- Enhanced Purity:
High purity is something that Kamrollers and other producers are doing their best to improve, however, they have amazing levels now. The improvement of the manufacturing processes may lead to higher levels of purity which in turn may create opportunities in more sensitive applications such as semiconductors.
• Better Surface Finishes:
Since the silica rollers available in the market today have a relatively very smooth surface, there is the possibility of further enhancements in the polishing processes to produce an even smoother surface. This way, friction and wear would be minimized even more along with improvement in the performance and life of rollers.
- Increased Thermal Resistance:
Such a feature as thermal stability is typical of silica rollers due to the fact that they are made of silica, which is a heat-resistant material. However, the aim of research and development is to possibly go further in the aspect of heat resistance. Consequently, it could be possible to use the proposed models in applications with gradually increasing temperature conditions.
- Tailored Material Properties:
Future silica rollers with certain characteristics may be designed. Consider rollers that for a given application have been designed to have better chemical resistance or have their thermal expansion coefficients altered. Thus, it will be possible to open up entirely new opportunities with such a level of personalization.
- Advanced Coatings:
New advanced coatings which may be used specifically for fused rollers may be introduced in the future. Besides, the coatings can possess enhanced surface durability, reduced surface friction, or even auto-lubrication characteristics.
Conclusion:
Due to our commitment to state-of-the-art production processes and quality control, you are assured that the rollers supplied to you will meet and/or exceed the requirements of your application. To view our range of sizes, purities, and surface treatments please select from one of the categories below and select the perfect match for your needs. Get the best out of the fused silica roller in your operations through the help of KAMROLLER to discover the possibilities. Call us now and let us elaborate on the specifics of the job you want us to do!
Read more: Buy Fused Silica Ceramic Roller | High-Quality & Reliable