Silicon Steel Bottom Annealing Roller: Essential Guide
2024.07.06admin
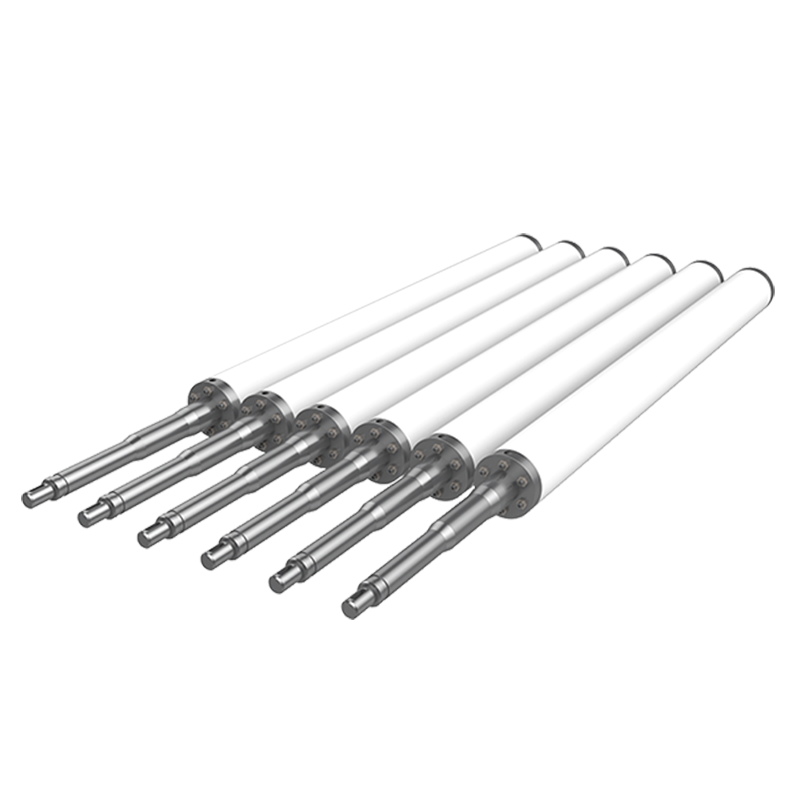
Role of Silicon Steel Bottom Annealing Rollers in Electrical Steel Production
In this article, I will put shed over silicon steel bottom annealing roller which may be considered as the backbone of the continuous annealing line as it is hardly noticed. In the process of annealing, rollers are quite crucial in helping to support and feed the steel coil into the furnace. In this case, the performance is a direct reflection of the final product’s consistency as well as quality.
- Silicon steel is a material that is the backbone of all the above mechanisms. Silicon steel is used in transformers, motors, and generators commonly. Due to its high magnetic features, it aids in power consumption. However, silicon steel has one major process that has to be undergone to realize its full potential, this process is known as annealing.
- The process of annealing involves heating and cooling of steel in a manner that positively alters its structure as regards magnetic properties. For the right level of softness, low hysteresis loss that is the energy lost during the cycling of magnetization this process is crucial.
Basic Overview of Silicon Steel Bottom Annealing Rollers:
The silicon steel bottom annealing roller is one of the most important factor in the process of manufacturing the electrical steel. While in the process of annealing, these rollers help in holding and guiding the silicon steel coil through the hot furnace. The quality and standard of the final product are dependent on the performance of the latter.
The Annealing Process and Its Importance:
It has great magnetic properties and applied in transformers, motors and generators which make it one of the strategic materials. It needs to be annealed to get the full potential out of it, though. The steel’s microstructure is refined by this regulated heating and cooling process, improving its magnetic characteristics by:
- Increasing softness
- Decreasing of the energy losses due to hysteresis (energy dissipated during the magnetization and demagnetization)
- Improving grain structure
How do Bottom Annealing Rollers Contribute?
The silicon steel bottom annealing roller is located inside the annealing furnace and plays an important role in:
- Even Heat Distribution:
They offer constant and even heating of the material by means of transferring the heat to the steel coil. This means that the final product will be the best as regards the magnetic performance it will display.
- Dimensional Stability:
These rollers also do not change shape even at high temperatures and thus, prevent deformation of the steel coil. It ensures that what you are producing is flat and of the correct dimension every time.
- Reduced Surface Defects:
Due to the smooth surface of the rollers, the steel coil is not easily likely to be scratched or have other marks on it. This is important in order to maintain the end use functionality of the finished electrical steel component.
In the continuous annealing line, annealing rollers can be said to be the backbone but rarely get the recognition they deserve. Their efficiency depends on the quality of the final electrical steel product and the rate of production. Electrical steel is an important material in today’s electrical network system.
The Science of Annealing and Silicon Steel:
A type of electrical steel is called silicon steel which contains a small amount of silicon, normally between 1 to 3 percent. 5%. This element alters the crystal structure of the steel; it makes eddy current losses to reduce – the energy loss that is caused by the currents that are induced and also improves its magnetic permeability that is, the ability of the material to allow the flow of magnetic fields. Further improvements of the steel microstructure are achieved by the annealing process. The steel is heated to a certain temperature in this process and this makes the grains which were earlier distorted to recrystallize. Thus, the grain structure is refined and the material becomes more uniform, which enhances the magnetic properties.
Properties of High-Performance Silicon Steel Bottom Annealing Rollers:
The condition of rollers of a continuous annealing line is one of the most critical factors that define the line’s efficiency. These rollers are used in extreme conditions; hence there are some properties that the rollers must possess to ensure that they perform to the best of their abilities and to produce quality products. Now let’s examine the essential features of annealing rollers with good performance:
- High Thermal Conductivity:
Heat is transferred very efficiently. In this case of continuous, uniform annealing, heat transfer from the furnace environment to the steel coil must occur through the rollers. The finished product is likely to have better magnetic qualities in this case.
- Wear Resistance:
Due to rubbing against the steel coil, there is general wear and tear that is incurred. A good wear resistance is a characteristic of high performance rollers that helps minimize on the time taken to replace and maintain the rollers.
- Dimensional Stability:
This has an implication of having to maintain the exact form even at high temperatures. This ensures that the steel coil does not twist or roll to the side because of the better dimensional stability of the rollers.
- Anti-Decarburization:
The properties of the steel coil could be affected by carbon maybe coming out of the surface at high temperatures. These features or phenomena do not affect special coatings or material compositions on high performance rollers and therefore do not affect the surface of the roller.
- Resistance to Oxidation:
Among the possible effects of high temperature is oxidation or the growth of a surface oxide layer. Improved oxidation of rollers prevents the formation of oxides and thus they cannot interfere with the heat transfer and rollers’ performance.
As a result, to the manufacturing of high quality electrical steel the high-performance silicon steel bottom annealing roller plays a critical role because they always possess the following desirable characteristics.
Why to Choose the Kamroller annealing Roller?
- Quality:
These Rollers are manufactured to meet the highest quality standards and rigorously tested for reliability, ကြာရှည်ခံမှု, and consistence in performance.
- Technical know-how:
Enabling the clients with the knowledge of material science and engineering, we provide consultation in choosing the right set of rollers for the required application.
- Global Reputation:
Kamroller has thus developed a good market that deals with the supply of quality, reliable and customer-focused annealing rollers to industrial producers globally.

Applications of Silicon Steel Bottom Annealing Rollers:
It is then understood that bottom annealing rollers made of silicon steel are required for the manufacturing of electrical steel at all stages. These are vital in developing high-quality and durable products due to their characteristics such as handling high temperature, uniform heating and lower tendencies of wearing out. A closer look at their main uses is provided below:
Production of Electrical Steel:
- Function:
The silicon steel coils are rolled and conveyed through the high-temperature furnace during the annealing process by means of these rollers which are the worker horses of the continuous annealing lines.
- Uniform Annealing:
The process of uniform annealing ensures that the finished product has uniform magnetisation through heating the entire steel coil by the use of rollers.
- Better Core Loss Characteristics:
Thus, allowing proper recrystallization, the rollers help reduce core losses in the electrical steel that is finished, which means that transformers and motors will consume less power.
Transformer Core Manufacturing:
• Function:
In this case, the rollers are used to work on separate silicon steel sheets before they are piled up and wound into transformer cores during the pre-annealing process.
• Advantages:
Enhanced Magnetic qualities:
The rollers ensure that the steel sheets are well heat treated and this leads to the enhancement of the magnetic properties which are very vital for the efficiency of a transformer.
Dimensional Accuracy:
It is, therefore, beneficial to have a well-assembled and effective transformer core, rollers’ dimensional stability assists in maintaining the steel sheets’ thickness and flatness.
Maintenance tips for silicon steel bottom annealing rollers:
The continuous annealing line is mainly equipped with a silicon steel bottom annealing roller. The roughest rollers, still, need regular maintenance from time to time to make sure that everything is fine and the device works at the highest possible level. The following are important upkeep procedures:
- Frequent Cleaning:
In order to avoid the hot coil’s uneven heating and to prevent the damaging of the steel coil it is recommended that the roller is cleaned and any scale or debris is removed from the surface.
- Lubrication:
To decrease the wear and tear and to minimize the friction between the steel coil and the roller, one should follow an adequate lubrication program.
- Periodic Inspections:
Check for signs of wear on the rolling surface at regular intervals in the form of surface; crack, pin or excessive wear. If diagnosis is done early, then the steel coil is not affected and can be replaced as soon as possible.
- Appropriate Handling:
During installation and removal of the rollers ensure they are not damaged by applying the right procedures.
- Therefore, it is recommended to adhere to the following tips that can help you greatly extend the service life of your bottom annealing rollers and minimize the time required for their replacement, as well as guarantee the stable production of high-quality electrical steel.
- It is advisable to contact a reputable roller maker, Kamroller to get more information about the roller techniques
Choosing the Best Material: Grain Stabilized as Compared to Non-Grain Oriented
The type of silicon steel bottom annealing rollers that you need for your specific application will depend on the following. Here’s a little explanation:
- Grain-stabilized:
These are some of the benefits; they have good wear and tear resistance, good dimensional accuracy and high temperature strength.
- Grain-free (NGO):
Advantages: economical.
Grain stabilized rollers are suitable for use in complicated operations. NGO rollers might be cheaper than the wheeled ones for use in less strenuous conditions.
Conclusion:
This is when one needs to work with a reputable manufacturer, KAMROLLER for a better performance and a longer lasting product. When it comes to your silicon steel bottom annealing roller requirements, we are your one stop shop. Thanks to our stock, we ensure that the right high-performance roller for your specific case shall be brought to your notice. Call us now and let us know your needs and how we can assist you in getting the highest possible yield of electrical steel.
Read more: Fused Silica Tweel: A Comprehensive Guide to Fused Silica