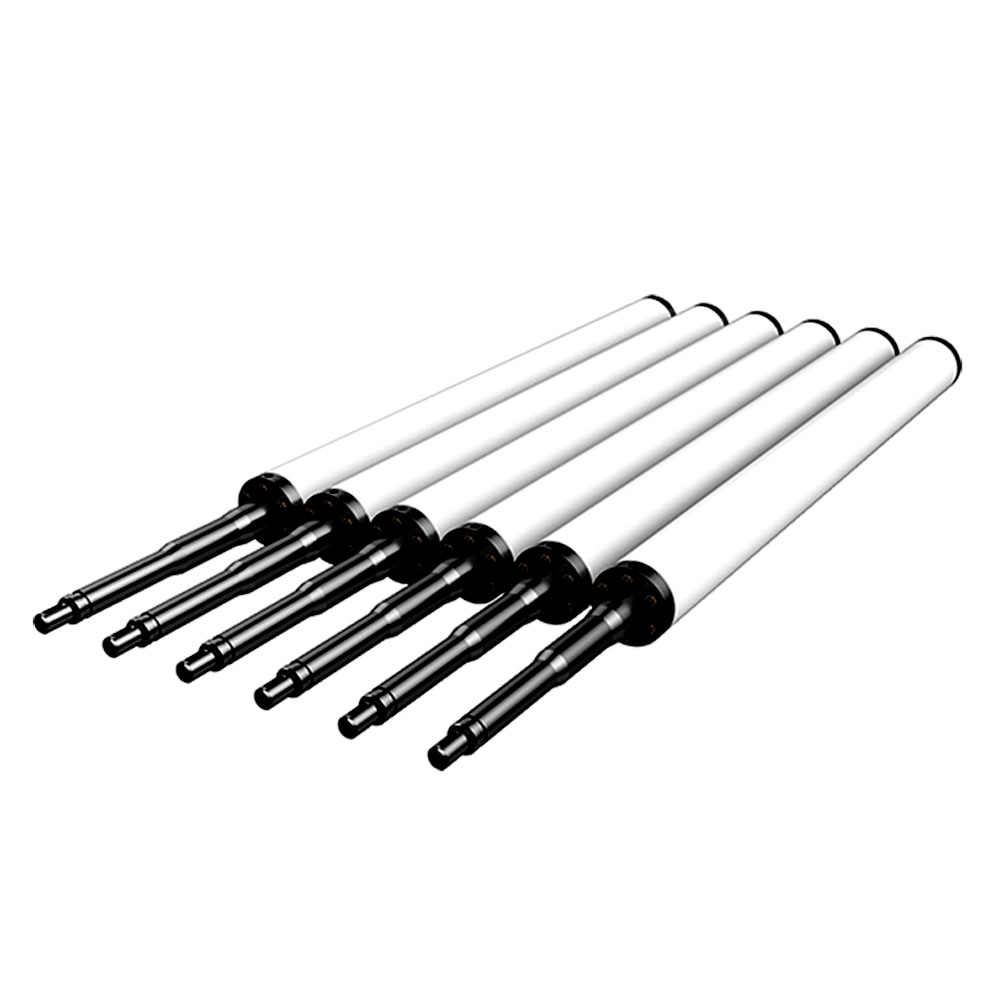
Silicon Steel Bottom Annealing Roller
✦ Excellent High Temperature Resistance, Melting Point Up To 1800°C, Low Thermal Expansion Coefficient, Excellent Thermal Stability
✦ Excellent Mechanical Strength: High Compressive Strength, Strong Bending Strength, Good Wear Resistance
✦ Excellent Thermal Shock Resistance: Good Thermal Shock Resistance, Not Easy To Crack, Greatly Extending The Service Life
✦ Strong Chemical Stability, Strong Corrosion Resistance, Excellent Chemical Stability, Strong Resistance To Acid And Alkali Erosion
✦ Precision Molding Capability: High Precision, Smooth Surface, Good Dimensional Accuracy
♦ Environmentally friendly and pollution-free: no harmful substances, green environmentally friendly materials, clean production process
Product Image
Product Certificate
-
DESCRIPTION
-
SPECIFICATION
-
FQA
The Silicon Bottom Roller is meticulously designed for bottom annealing furnaces where silicon steel sheets undergo vital heat treatment. Boasting exceptional heat resistance, the roller endures extreme temperatures and thermal cycling intrinsic to the annealing process. This design ensures consistent and controlled heat distribution, leading to precise and reliable results.
The precision machining and surface finish of the Silicon Bottom Roller minimize surface imperfections and ensure smooth, uniform contact with the silicon steel sheets. This guarantees even heat transfer, reducing the risk of surface irregularities and distortions in the annealed material. Ultimately, it enhances the quality and performance of the silicon steel sheets.
Features
Silicon steel annealing rollers are ideal for demanding annealing processes like steel manufacturing. They facilitate the annealing of high-temperature silicon steel sheets, operating within a temperature range of 600-950°C. The roller table is engineered to meet stringent process requirements and is used in conjunction with Kamroller’s proprietary patented shaft end technology, ensuring smooth and predictable delivery.
Low Thermal Expansion: With a low coefficient of thermal expansion, these rollers maintain their shape and dimensions even under rapid temperature changes, ensuring precise control over the annealing process and preventing deformation of the steel sheets.
Optimized Surface Finish: The rollers are engineered with optimized surface finishes to minimize surface defects on the annealed steel sheets, ensuring superior surface quality and reducing the need for post-processing.
High Wear Resistance: Designed to withstand the wear and abrasion encountered during steel processing, these rollers offer high wear resistance, resulting in extended service life and reduced maintenance requirements.
Efficient Heat Transfer: Engineered to maximize heat transfer efficiency, the rollers facilitate rapid and uniform heating of the steel sheets, resulting in shorter annealing cycles and increased production throughput.
Enhanced Productivity: By ensuring consistent and reliable annealing performance, these rollers contribute to increased productivity in steel processing facilities, allowing for higher production volumes and improved operational efficiency
Applications of Silicon Steel Bottom Annealing Roller:
Electrical Steel Production: Used in the manufacturing of electrical steel, also known as silicon steel, these rollers support the annealing process to enhance the magnetic properties and core loss characteristics of the steel sheets.
Transformer Core Manufacturing: Employed in the production of transformer cores, where annealed silicon steel sheets are stacked and wound to form the core assembly. The rollers facilitate the annealing process to ensure uniformity and consistency in magnetic properties across the core.
Motor and Generator Components: Utilized in the fabrication of motor and generator components, such as rotor and stator laminations, where annealed silicon steel sheets are used to improve energy efficiency and reduce core losses.
Industrial Equipment: Applied in various industrial equipment and machinery requiring high-performance silicon steel components, including magnetic circuits, solenoids, and electromagnetic devices.
Energy Transmission and Distribution: Used in electrical transmission and distribution systems, where silicon steel components are employed in transformers, reactors, and other power equipment to improve energy efficiency and reduce losses during power transmission.
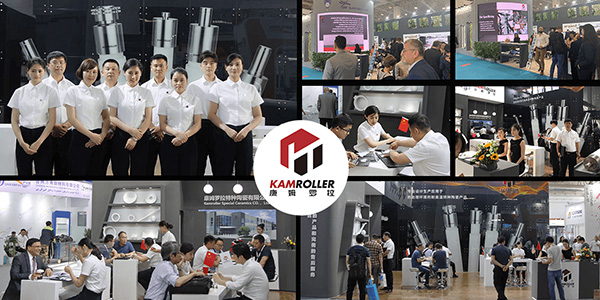
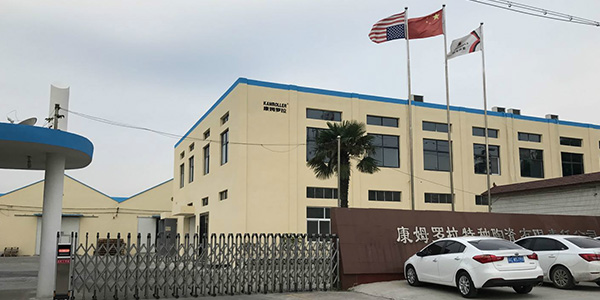
What is a Silicon Steel Bottom Annealing Roller?
A Silicon Steel Bottom Annealing Roller is a specialized component used in the annealing process of silicon steel sheets. The roller supports and moves the steel sheets through the annealing furnace, ensuring uniform heating and cooling, which improves the material's magnetic properties.
What is Annealing?
Annealing is a heat treatment process used to alter the physical and sometimes chemical properties of a material. In the case of silicon steel, annealing relieves internal stresses, refines the grain structure, and enhances magnetic properties, making it suitable for use in electrical transformers and motors.
Why is Silicon Steel used in Annealing Rollers?
Silicon steel is used in the manufacturing of annealing rollers due to its excellent magnetic properties, high electrical resistance, and ability to maintain stability at high temperatures. These properties are essential for ensuring efficient and uniform heating during the annealing process.
What are the Benefits of Using Silicon Steel in Annealing Rollers?
High Magnetic Permeability: Improves the efficiency of transformers and motors. Low Core Loss: Reduces energy loss in electrical applications. High Electrical Resistance: Minimizes eddy current losses. Thermal Stability: Maintains performance and shape at high temperatures.
How Does a Silicon Steel Bottom Annealing Roller Work?
The roller supports the silicon steel sheets as they pass through the annealing furnace. It ensures even exposure to heat, allowing the material to undergo controlled heating and cooling cycles. This process enhances the steel's magnetic properties and reduces internal stresses.
What are the Key Features of a High-Quality Silicon Steel Bottom Annealing Roller?
Бат бөх чанар: Made from materials that can withstand high temperatures and mechanical stress. Precision Engineering: Ensures uniform heating and cooling of the silicon steel sheets. Low Maintenance: Designed for prolonged use with minimal maintenance requirements.
How to Maintain a Silicon Steel Bottom Annealing Roller?
egular Inspections: Check for wear and tear, and ensure the roller is clean and free of debris. Lubrication: Apply appropriate lubricants to reduce friction and wear. Alignment Checks: Ensure the roller is properly aligned to avoid uneven heating of the steel sheets. Replacement: Replace worn-out rollers promptly to maintain the efficiency of the annealing process.
Common Problems and Solutions
Uneven Heating: Ensure the roller is clean and properly aligned. Check the furnace settings. Wear and Tear: Regularly inspect and replace the roller as needed. Friction Issues: Use appropriate lubricants and check for proper lubrication schedules.
Applications of Silicon Steel Bottom Annealing Rollers
Electrical Transformers: Enhance the magnetic properties of silicon steel used in transformer cores. Electric Motors: Improve efficiency and performance of motors by enhancing the steel's magnetic properties. Generators: Ensure optimal performance by using high-quality silicon steel with improved magnetic properties.
What to Look for When Choosing a Silicon Steel Bottom Annealing Roller?
Material Quality: Ensure the roller is made from high-grade silicon steel. Manufacturer Reputation: Choose a reliable manufacturer with a track record of producing high-quality annealing rollers. Compatibility: Ensure the roller is compatible with your specific annealing furnace and process requirements. Cost-Effectiveness: Consider the long-term benefits and maintenance costs when evaluating the price.