How Fused Silica Ceramic Rolls Are Made
2024.06.10hqt
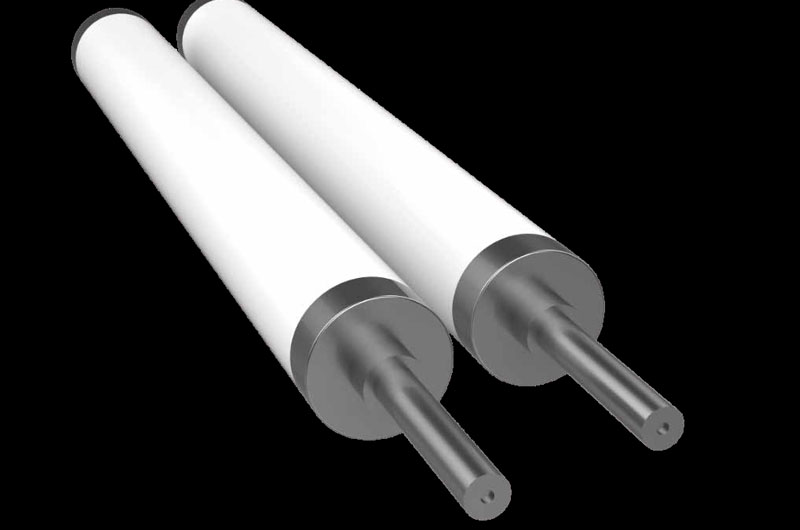
Manufacturing Fused Silica Ceramic Rollers
Introduction to Fused Silica Ceramic Rollers
Fused silica ceramic rollers are critical components designed for high-temperature applications, widely used in the glass manufacturing, ceramic firing, and metal heat treatment industries. Their main features include:
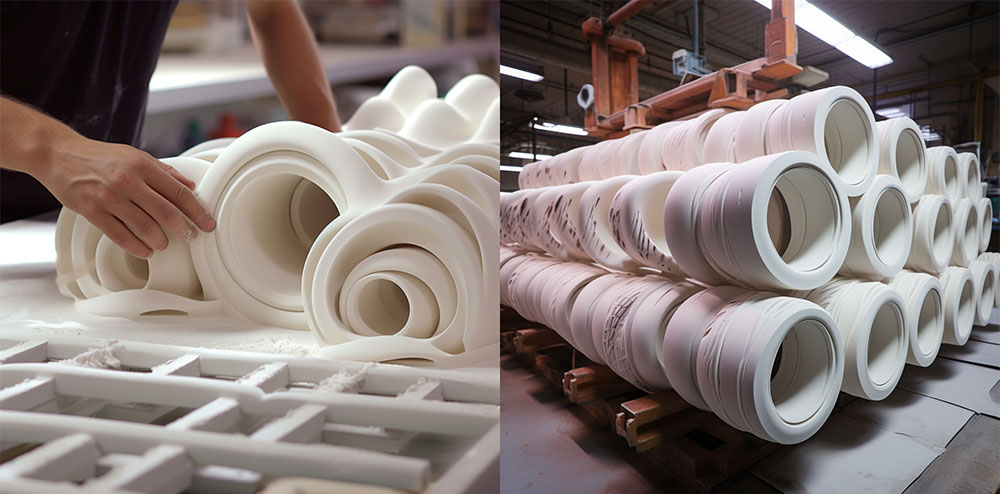
- Wear Resistance: Fused silica ceramic rollers exhibit excellent wear resistance, allowing them to be used in high-temperature environments for extended periods without significant wear.
- Corrosion Resistance: These rollers possess good resistance to various chemicals, making them suitable for harsh chemical environments.
- High-Temperature Stability: Fused silica ceramic rollers have outstanding thermal stability at high temperatures, maintaining their physical and chemical properties under extreme temperature conditions.
Manufacturing Process
- Raw Material Selection: High-purity quartz sand is chosen as the primary raw material to ensure the purity and performance of the final product.
- Mixing: The quartz sand is mixed with a suitable binder and other additives to form a uniform mixture.
- Forming: The mixture is pressed into the preliminary shape of the roller using a mold. This step requires precise control of pressure and time to ensure the density and dimensional accuracy of the formed roller.
- Drying: The formed roller undergoes a drying process to remove excess moisture. This step is usually conducted at low temperatures to prevent cracking of the roller body.
- Firing: The dried roller is placed in a high-temperature kiln for sintering, achieving the desired hardness and heat resistance. The temperature and duration of the firing process need to be precisely controlled to ensure the quality of the roller.
- Cooling and Post-Processing: After firing, the roller is slowly cooled to prevent internal stresses. Subsequently, necessary mechanical machining and surface treatments are performed to achieve the final dimensions and surface quality requirements.
Applications
Fused silica ceramic rollers are widely used in the following fields:
- Glass Manufacturing: Used on glass production lines to transport and support high-temperature glass, ensuring the glass’s flatness and quality.
- Ceramic Firing: Used in the ceramic production process to transport and support high-temperature fired ceramic products.
- Metal Heat Treatment: Used in the metal heat treatment process to transport and support high-temperature metal workpieces, ensuring the shape and quality of the workpieces.
Material Selection
Silica Kokohu
- Fused silica is the primary material, known for its high purity and high melting point. Its high purity ensures excellent performance in the final product, especially under high-temperature conditions. Additionally, fused silica has a very low thermal expansion coefficient, which prevents deformation with temperature changes, enhancing the durability and reliability of the product.
Binders
- Organic glue or silicone resin is commonly used as a binder. Organic glue offers strong adhesive properties, effectively bonding fused silica particles together and forming a solid structure upon curing. Silicone resin, on the other hand, provides exceptional high-temperature resistance, maintaining stability in high-temperature environments while offering good mechanical strength and chemical resistance. The use of these binders ensures that the material retains its excellent properties under various complex conditions.
Preparation Process
Material Pretreatment
- Mix fused silica powder with the binder and ensure uniform dispersion.
Molding
- Use injection molding or pressing techniques to fill the pretreated material into molds, applying pressure to form the desired shape.
Sintering
- Place the molded quartz ceramic rollers into a high-temperature furnace for sintering. This step eliminates residual binder and ensures the ceramic materials are firmly bonded.
Surface Treatment
- Perform surface processing on the sintered rollers, including grinding and polishing, to ensure smoothness and precision of the surface.
Quality Control
Dimensional Measurement
- Use precision instruments to measure the diameter, length, and roundness of the rollers, ensuring they meet the specified requirements.
Surface Inspection
- Conduct visual inspections or use surface defect detection equipment to check the surface quality of the rollers, ensuring they are free of cracks, bubbles, and other defects.
Performance Testing
- Perform tests for wear resistance, corrosion resistance, and high-temperature stability to ensure the rollers perform well in actual applications.
Application Areas
Glass Industry
- Used for the conveyance and processing of glass sheets and glass tubes on glass production lines.
Metal Heat Treatment
- Utilized for the transportation and support of metal sheets during continuous annealing and quenching processes.
Advantages
High Temperature Resistance
- Capable of operating stably for extended periods in high-temperature environments.
Wear Resistance
- Exhibits excellent wear resistance, thereby extending its service life.
Corrosion Resistance
- Able to withstand corrosion from acidic and alkaline substances, making it suitable for harsh environments.
Application Examples
Glass Production
- Utilized for the conveyance and processing of glass sheets and glass tubes.
Metal Processing
- Employed for the transportation and support of metal sheets during continuous annealing and quenching processes.