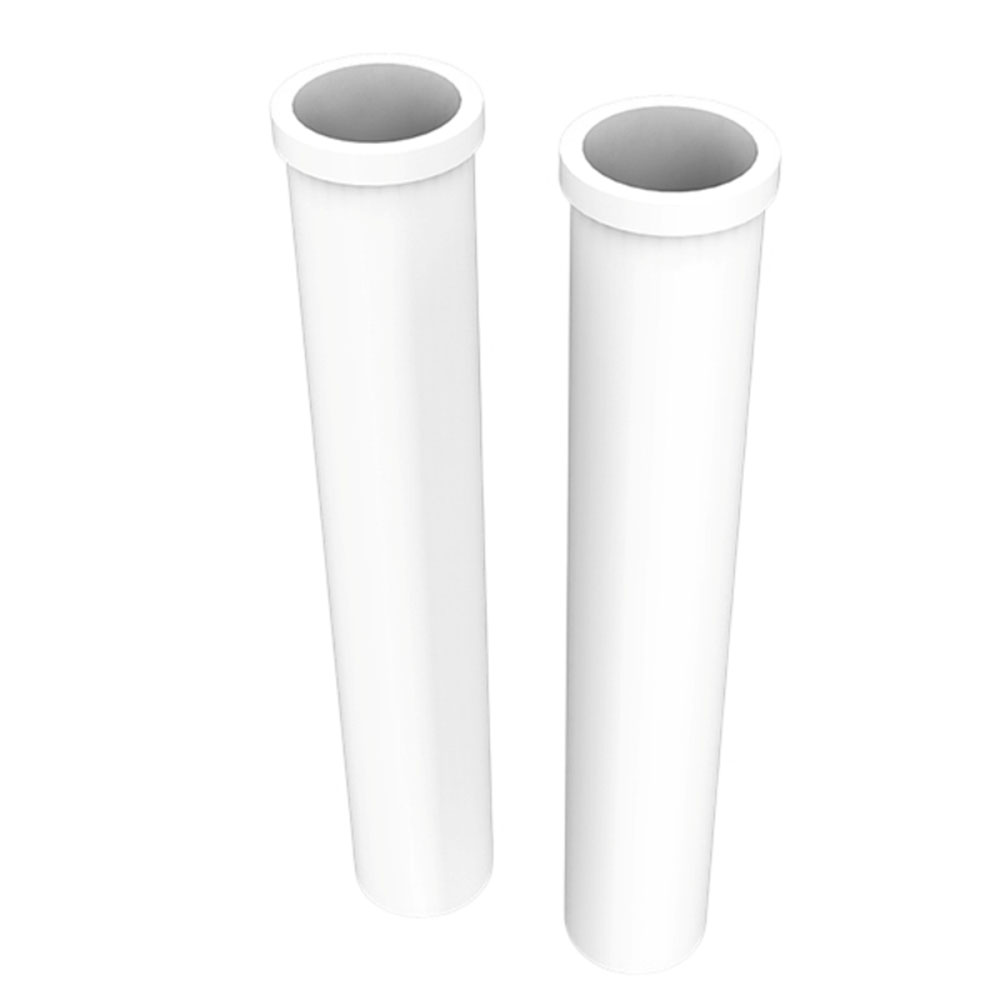
Quartz Powder,99.99% 500-1000µm
✦ Synonyms: quartz powder
✦ Formula: SiO2
✦ Cleanliness: 99,99%
✦Minimum quantity for sale: Excellent Optical Properties, Suitable For Laser Systems And Optical System Components
✦ Ultra-Low Thermal Expansion Coefficient: Extremely Low Thermal Expansion Performance, High Stability, Suitable For High-Precision Thermal Control Management
♦ Environmentally friendly and pollution-free: no harmful substances, green environmentally friendly materials, clean production process
Product Image
Fused Silica Barrels Certification
ISO9001,CE certification,RoHS environmental certification
Product specifications: Inner diameter: 20-150 mm, Length: 50-500 mm, Wall thickness: 2-10 mm
-
DESCRIPTION
-
SPECIFICATION
-
FQA
powder made of transparent quartz glass (ground fused quartz)
Powders made of transparent high-quality quartz glass are white powder with a mass fraction of SiO2 – 99.97 – 99.99% and a fraction size of 5 microns or more. The powder production technology ensures high chemical purity of the product.
Main characteristics of powders
Content of crystalline phases, % Coefficient of thermal expansion -1/degree K High chemical purity % Material density kg/m3
0 (3.5×10-7) SiO2-(99.97-99.99) 2.21×103
Powders are characterized by high chemical resistance to alkaline and acidic environments, as well as an increase in mechanical strength when heated.
SiO2 content – 99.99%
Impurity content,%:
Na K Cu Ti Ca Mn Mg Al Fe
3.09×10-4 5.5×10-4 0.05×10-4 1.7×10-4 1.0×10-4 0.18×10-4 9.3×10-4 7×10-4 1.51×10-4
The powder is intended for:
use as a filler for molding polymer press compositions used in the production of integrated circuits in microelectronics and ensures their operation in extreme conditions.
production of refractory products intended for laying out critical parts of glass furnaces: basins, ducts, screens, etc.
used as a material in the manufacture of thermal and corrosion protection elements in chemical engineering, and metallurgy, capable of operating at temperatures above 10000C in contact with molten glass and molten metals.
production of covers in the manufacture of high-temperature induction furnaces.
As a key material in the semiconductor industry and optical field, fused quartz barrels have important application value and development prospects. By optimizing the manufacturing process and improving product quality, we can better meet the needs of different fields and promote the development and innovation of related industries.
What are Fused Silica Barrels
Fused Silica Barrels: An important material used in the semiconductor industry with high purity and excellent heat resistance
What are the advantages of fused silica barrels?
- High temperature stability: Able to withstand extremely high temperatures without melting or deforming - Chemical inertness: Good corrosion resistance to a variety of chemicals - Optical transparency**: It has excellent optical transparency and is suitable for optical processing and detection. - Precision processing**: It can be precisely processed into various shapes to meet different needs.
What are the main application areas of fused silica barrels?
- Semiconductor manufacturing**: used to manufacture key components of semiconductor process equipment such as lithography machines and thin film deposition equipment. - Optical instruments**: suitable for manufacturing lenses and optical components of optical equipment such as telescopes and spectrometers. - Chemical experiments**: as storage containers for chemical reagents, they withstand high temperatures and corrosive substances.
What is the manufacturing process of fused silica barrels?
- Melting**: Heating high-purity silica material to a molten state. - Molding**: Molding the molten silica into a barrel shape using a mold or precision machining technology. - Annealing**: Eliminating internal stress by controlling temperature and time to improve the heat resistance and stability of the fused quartz barrel.
What are the common problems and solutions of fused quartz barrels? .
- Thermal shock cracks**: Cracks appear under rapid temperature changes. - Solution**: Optimize the annealing process to improve the thermal stability of the fused quartz barrel. - Chemical erosion**: Damage caused by corrosive substances such as strong acids and alkalis. - Solution**: Improve the surface coating or select materials with stronger corrosion resistance. - Shape inaccuracy**: Shape deviation or irregularity that occurs during the manufacturing process. - Solution**: Optimize the manufacturing process, strengthen quality control, and ensure product accuracy. - Internal bubbles**: Gases present in the material are trapped in the barrel, affecting its service life and performance. - Solution**: Optimize the material purification process, reduce gas residues, and improve material quality.
What is the maintenance method of fused quartz barrel?
- Regular cleaning**: Use a special cleaning agent to clean the surface to remove sediment and dirt. - Avoid collision**: Handle with care and avoid collision with hard objects to prevent surface scratches or damage. - Proper storage**: Avoid long-term exposure to high temperature or humid environment, and choose a dry and ventilated storage location. - Regular inspection**: Regularly check the surface for cracks or damage, and repair or replace it in time