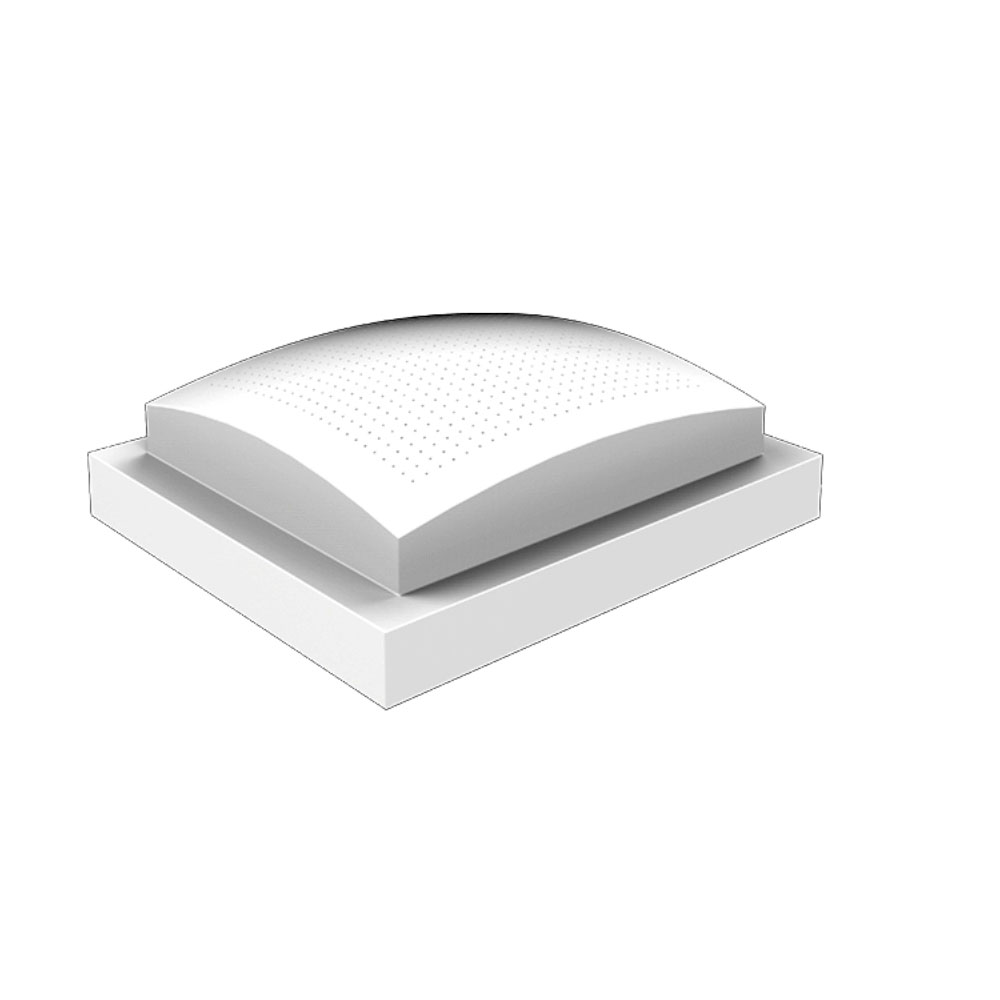
Fused Silica Ceramic Mold For Glass Bending
✦ High temperature resistance: – Outstanding high temperature resistance, suitable for high temperature environment during glass bending process. – Safe and reliable, not easy to deform or break, ensuring the stability of production process.
✦ Precision machining: – Using advanced machining technology to ensure smooth mold surface and improve the accuracy of glass molding, – Providing a variety of specifications and sizes to meet the processing needs of different glass products.
✦ Wear and corrosion resistance: – The mold material has excellent wear resistance and corrosion resistance, which can be used stably for a long time and reduce replacement costs.
✦ High-quality materials: – Made of high-quality fused quartz ceramic material, ensuring the surface smoothness and transparency of the molded glass.
✦ Highly customized: – Support customers’ personalized customization needs and provide customized mold manufacturing services according to specific processing requirements.
✦ Reliability:- After strict quality control and testing, the product quality is reliable and the stable performance is more guaranteed.
Product Image
Product Certificate
-
DESCRIPTION
-
SPECIFICATION
-
FQA
The Fused Silica Ceramic Mold is designed to withstand extreme heat. This makes it ideal for glass manufacturing, metal casting, kilns, furnaces, and other high-temperature processes. Its unique composition ensures minimal thermal expansion, preventing cracking or distortion, even under rapid temperature changes.

With its dense and non-porous structure, the Fused Silica Ceramic Brick exhibits remarkable resistance to thermal shock, chemical corrosion, and abrasion. This ensures a prolonged service life and consistent performance, while also reducing downtime and maintenance costs. The Brick’s smooth and flat surface provides excellent contact and stability when used as a lining or support material.
The Fused Silica Ceramic Mold for Glass Bending represents the pinnacle of precision engineering, meticulously crafted to meet the exacting demands of glass forming processes. Engineered with cutting-edge technology and expertise, this specialized mold plays a pivotal role in shaping and bending glass with unparalleled accuracy and reliability. Designed to withstand the extreme temperatures and thermal cycling inherent in glass bending applications, the Fused Silica Ceramic Mold ensures consistent and precise results, making it an indispensable tool in the production of high-quality glass products.
Applications of the Fused Silica Ceramic Mold for Glass Bending
The Fused Silica Ceramic Mold for Glass Bending finds wide application in the glass industry, baita ... Ere:
Architectural Glass: Used in the production of curved and bent glass panels for architectural applications, such as windows, doors, and skylights
Automotive Glass: Employed in the manufacturing of curved windshields, side windows, and rear windows for automobiles, ensuring precise bending and shaping for optimal fit and functionality.
Automotive Glass: Employed in the manufacturing of curved windshields, side windows, and rear windows for automobiles, ensuring precise bending and shaping for optimal fit and functionality.
Glass Furniture: Utilized for bending and shaping glass components used in furniture design, such as glass tabletops, shelves, and display cases.
Glassware and Tableware: Essential in the production of curved glassware and tableware items, including bowls, vases, and serving platters, for both commercial and residential use.
Why Trust Kamrollers
Kamroller has earned a reputation as a trusted leader in precision engineering, with a commitment to delivering high-quality products and exceptional customer service. Here’s why you can trust Kamroller for your Fused Silica Ceramic Mold for Glass Bending needs:
With extensive experience in glass forming processes, Kamroller possesses the knowledge and expertise to deliver high-quality molds tailored to the unique requirements of each customer.
Kamrollers provides tailored solutions to meet specific customer needs, offering personalized service and expert guidance throughout the process.
Every Silica Ceramic Mold undergoes stringent quality control checks to ensure precision, reliability, and performance, adhering to the highest industry standards.
Our Factory Image:
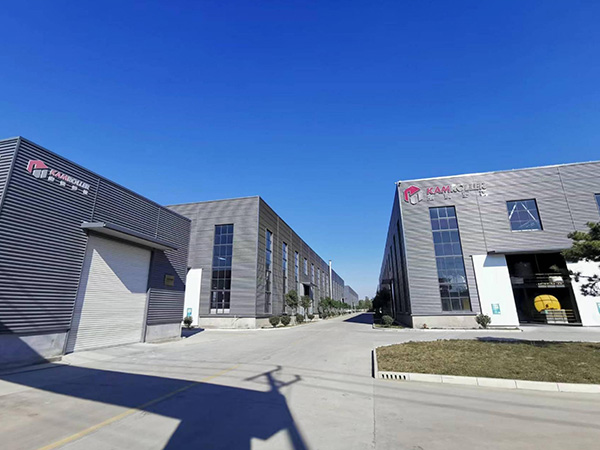
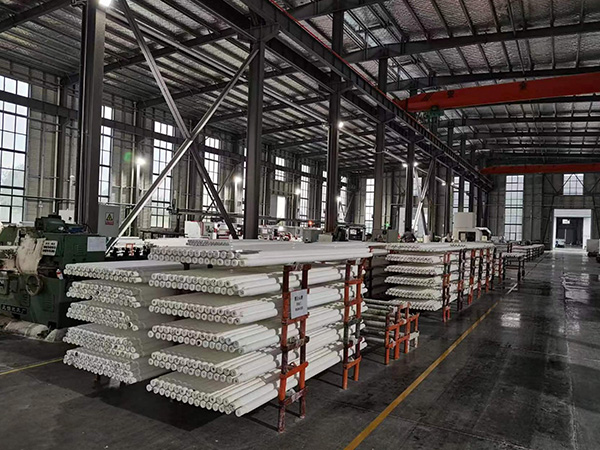
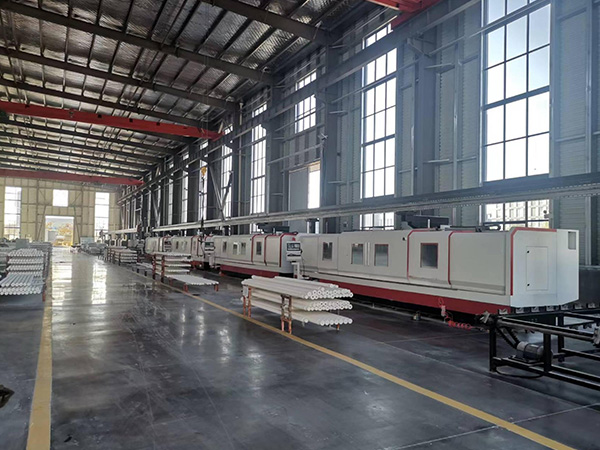
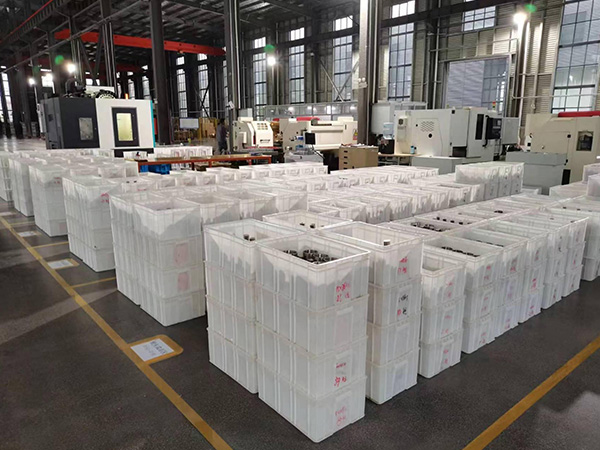
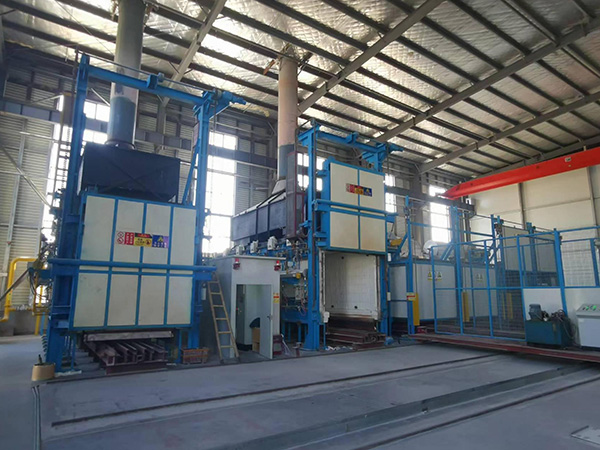
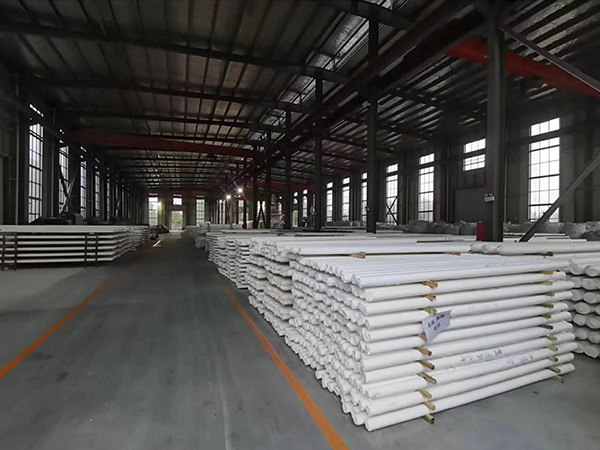
Packing Detail:
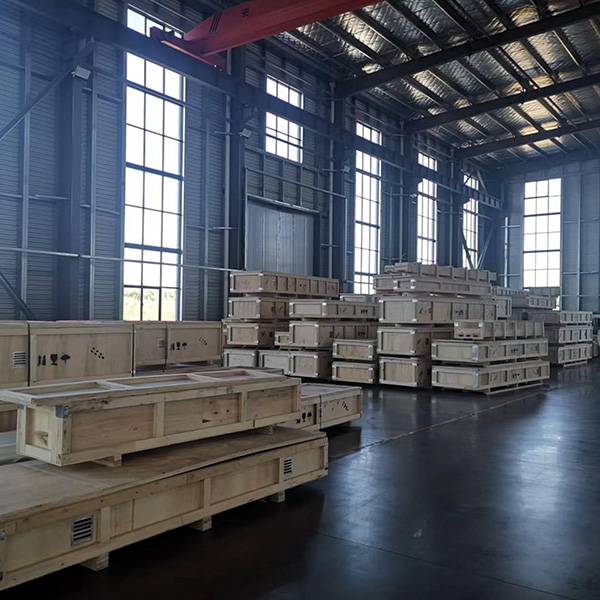
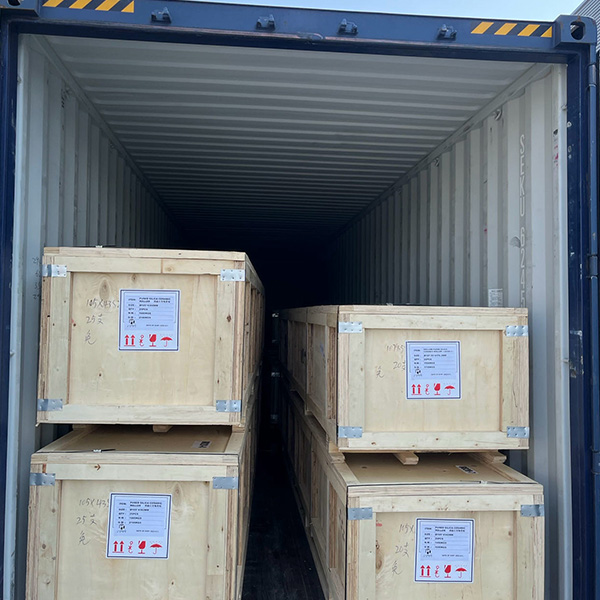
Kamrollers At The Exhibition:
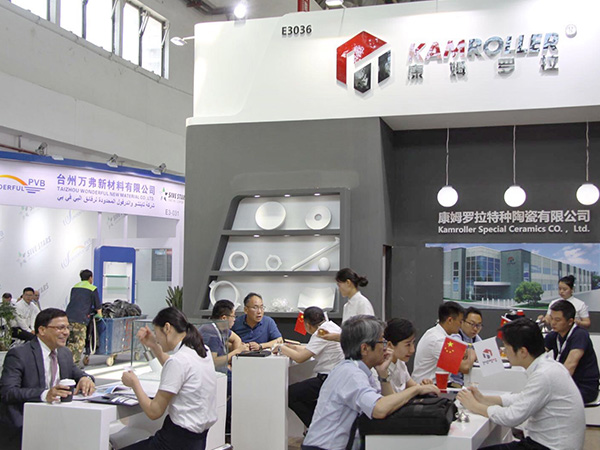
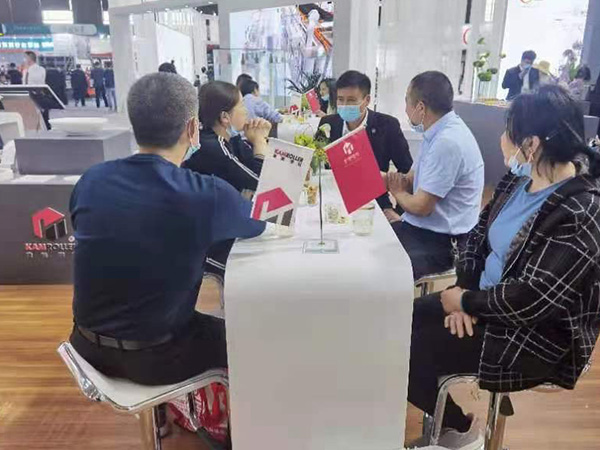
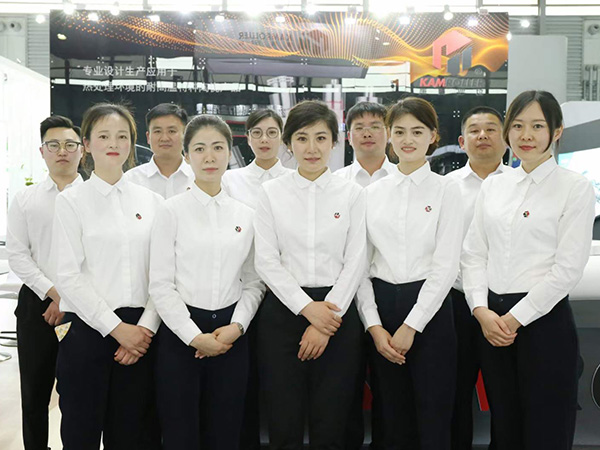
ISO Certificate:
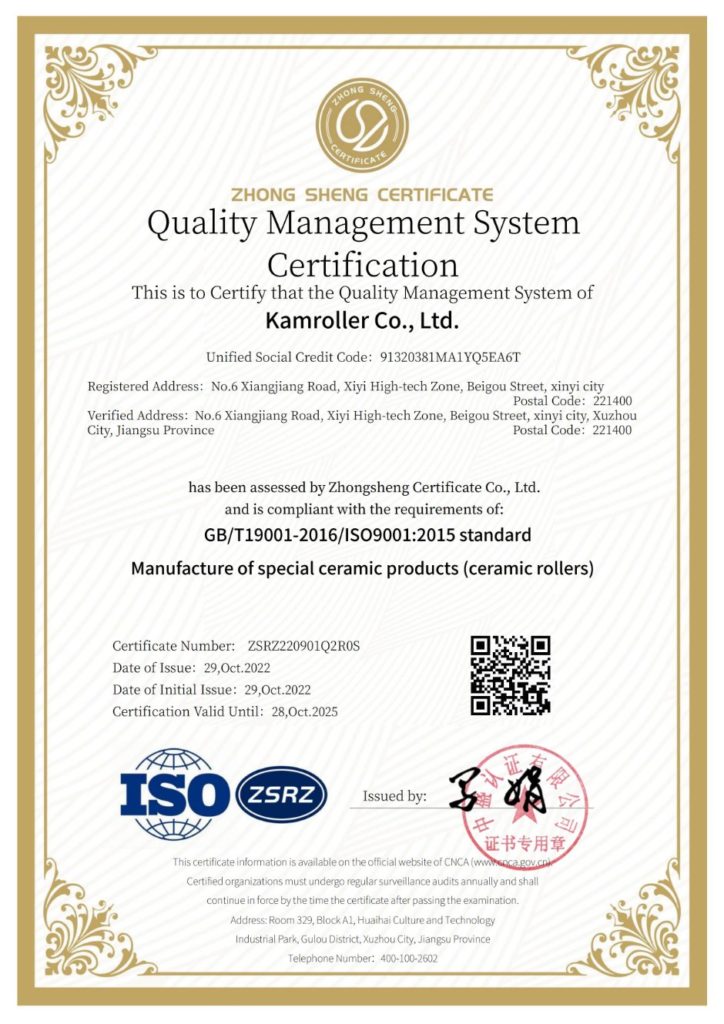
Fused silica ceramic molds are a critical tool in the glass bending industry, offering high temperature resistance, dilatazio termiko baxua, and excellent durability. Proper maintenance and handling are essential to maximize their lifespan and performance. For specialized applications, customized molds can be designed to meet specific needs.
What is a fused silica ceramic mold?
A fused silica ceramic mold is a type of mold made from high-purity silica (SiO2) that has been melted and cooled to form a solid, non-crystalline structure. These molds are used in the glass bending process to shape and form glass into specific contours and designs.
What are the advantages of using fused silica ceramic molds for glass bending?
High Temperature Resistance: Fused silica ceramic molds can withstand extremely high temperatures without deforming or breaking. Hedapen termiko baxua: They have a very low coefficient of thermal expansion, which means they maintain their shape and size even when exposed to high temperatures. Excellent Thermal Shock Resistance: These molds can endure rapid temperature changes without cracking or damaging. Smooth Surface: Provides a high-quality finish on the glass products. Iraunkortasuna: They are durable and can be reused multiple times.
How are fused silica ceramic molds made?
The production process typically involves melting high-purity silica powder and then cooling it rapidly to form a solid structure. This process can be done through various methods, such as slip casting, pressing, or machining, to achieve the desired mold shape.
What types of glass products can be made using these molds?
Fused silica ceramic molds are used to create a wide range of glass products, including automotive glass (windshields, side windows), architectural glass (curved glass panels), and specialty glass items (optical lenses, decorative glass).
How do you maintain and care for a fused silica ceramic mold?
Garbiketa erregularra: Keep the mold clean from any glass residue or contaminants. Proper Storage: Store molds in a dry, cool place to prevent moisture absorption and thermal shock. Handle with Care: Avoid dropping or striking the molds to prevent cracks and chips. Periodic Inspection: Regularly inspect the molds for any signs of wear or damage and repair or replace them as needed.
Can fused silica ceramic molds be customized?
Yes, fused silica ceramic molds can be customized to meet specific requirements for shape, size, and surface texture. Manufacturers can work with clients to design and produce molds that fit their unique glass bending needs.
What industries commonly use fused silica ceramic molds?
Automotive Industry: For shaping automotive glass components. Construction Industry: For bending architectural glass elements. Optical Industry: For precision glass lenses and optical components. Decorative Glass Industry: For creating artistic and decorative glass pieces.
What are the typical limitations of fused silica ceramic molds?
Cost: Fused silica ceramic molds can be more expensive compared to other types of molds due to the material's high purity and manufacturing process. Fragility: While they are durable under high temperatures, they can be brittle and may break if mishandled.
How do you choose the right fused silica ceramic mold for your application?
Consider factors such as the type of glass being bent, the temperature requirements, the complexity of the shape, and the expected production volume. Consulting with a manufacturer who specializes in fused silica ceramic molds can help ensure you select the appropriate mold for your needs.
Are there alternatives to fused silica ceramic molds?
Yes, alternatives include graphite molds, metal molds, and other types of ceramic molds. Each material has its own set of advantages and limitations, and the choice depends on the specific requirements of the glass bending process.