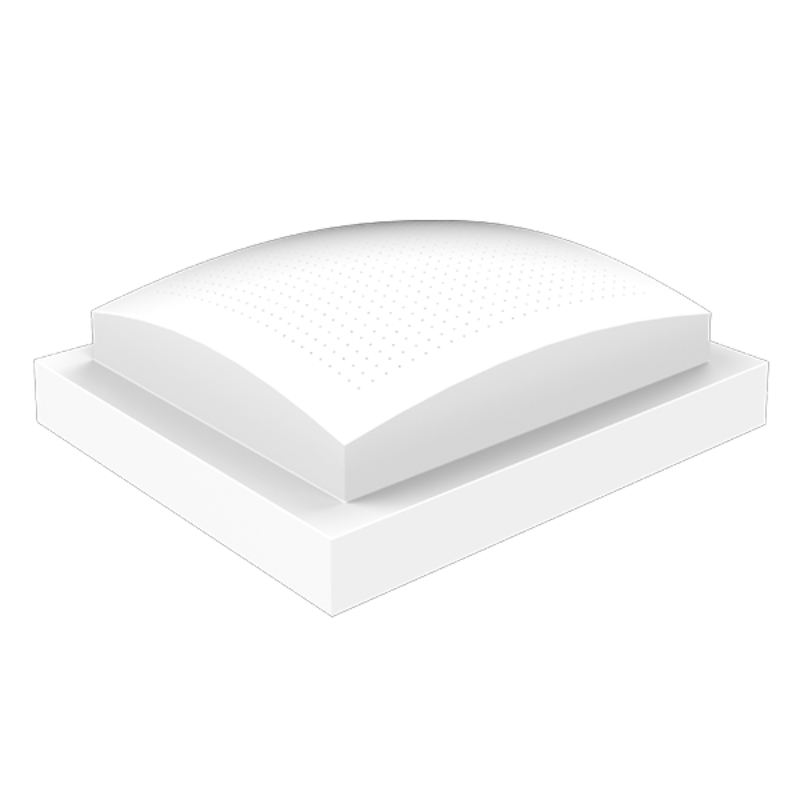
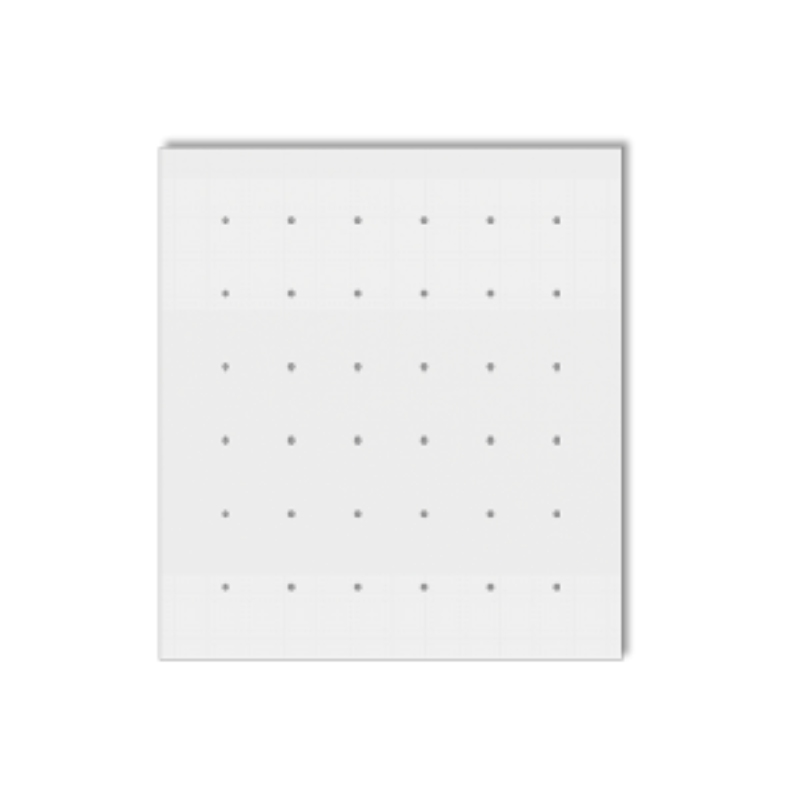
Fused Silica Ceramic Brick
✦ High Temperature Resistance: High Temperature Resistance Up To 3000 Degrees Celsius
✦ Thermal Shock Stability: Excellent Thermal Shock Resistance, Can Withstand Rapid Temperature Changes Without Cracking
✦ Chemical Stability Resistant To Acid And Alkali Corrosion, Used In Containers And Equipment For Corrosive Media In The Chemical Industry
✦ Mechanical Strength: High Tensile Strength And Compressive Strength, Wear And Erosion Resistance
✦ Thermal Insulation Performance: Avoid Heat Loss And Effectively Save Energy Costs
✦ Precision Machining: Precision Cutting And Customization According To Customer Needs, Customized Needs For Complex Shapes And Sizes
Product Center
Certificate
Chemical composition: SiO2 content ≥99%, density: 2.2~2.3g/cm³, compressive strength: ≥30MPa, linear expansion coefficient: 0.55~0.65×10^-6/°C, dimensional tolerance: ±1.0mm,Testing standards: GB/T 1866-2000, ISO 9385:1989《Fused silica bricks and blocks》, ASTM C820-96(2018)《Standard Specification for Fused Silica Brick》
-
DESCRIPTION
-
SPECIFICATION
-
FQA
Fused silica ceramic bricks are specialized refractory materials employed in a variety of high-temperature applications. These bricks are composed primarily of high-purity silica (SiO2) and are known for their excellent thermal shock resistance, low thermal expansion, and high thermal stability. Here’s an overview of their key characteristics, applications, and benefits:
Key Characteristics
✦ High Purity: Fused silica ceramic bricks are made from high-purity silica, ensuring minimal impurities that can affect performance at high temperatures
✦ Thermal Shock Resistance: These bricks can withstand rapid temperature changes without cracking or breaking, making them ideal for applications where temperature cycling is common.
✦ Low Thermal Expansion: The low coefficient of thermal expansion minimizes the risk of thermal stress and distortion, particularly under high-temperature conditions.
✦ High Thermal Stability: They maintain their structural integrity and mechanical properties even at very high temperatures.
✦ Chemical Inertness: Fused silica ceramic bricks are resistant to chemical attack from most acids and alkalis, enhancing their durability in aggressive environments.
✦ High Electrical Insulation: These bricks provide excellent electrical insulation properties, making them suitable for use in electrical and electronic applications.
Aplicaciones
✦ Glass Industry: Used in glass melting furnaces, forehearths, and other glass processing equipment due to their ability to withstand high temperatures and corrosive environments.
✦ Metallurgical Industry: Employed in furnaces and kilns for metal melting, refining, and processing, where thermal shock resistance and high-temperature stability are crucial.
✦ Ceramic Industry: Utilized in kilns and other high-temperature ceramic processing equipment.
✦ Solar Industry: Used in the production of solar panels and other solar energy applications due to their high purity and thermal stability.
✦ Electronics Industry: Applied in semiconductor manufacturing and other high-temperature electronic processes requiring excellent insulation and stability.
Benefits of Fused Silica Ceramic Brick
✦ Extended Service Life: High thermal shock resistance and stability contribute to longer service life, reducing maintenance and replacement costs.
✦ Energy Efficiency: Low thermal expansion and high insulation properties help improve energy efficiency in high-temperature processes.
Operational Safety: High chemical resistance and structural integrity enhance safety by minimizing the risk of brick failure and contamination of the processed materials.
Versatility: Suitable for a wide range of high-temperature applications across various industries, providing a versatile solution for refractory needs.
Fused Silica Ceramic Brick Composition
Fused Silica
- Pure Silicon Dioxide (SiO2)
- Fused silica is composed almost entirely of silicon dioxide (SiO2), providing exceptional purity and performance.
- Produced by Melting High-Purity Silica Sand
- This material is produced by melting high-purity silica sand in an electric furnace, resulting in a material that is both transparent and highly resistant to thermal shock.
- Transparent and High Thermal Stability
- Fused silica is renowned for its transparency in the ultraviolet, visible, and near-infrared spectra, as well as its high thermal stability, which makes it ideal for applications involving extreme temperatures.
Ceramic Materials
- Alumina (Al2O3)
- Alumina is a widely used ceramic material known for its excellent hardness, high thermal conductivity, and resistance to wear and corrosion.
- Mullite (3Al2O3·2SiO2)
- Mullite, a combination of alumina and silica, provides a balance of good thermal shock resistance, low thermal expansion, and high strength, making it suitable for high-temperature applications.
- Zirconia (ZrO2)
- Zirconia stands out for its high fracture toughness, excellent wear resistance, and the ability to withstand high temperatures, making it a crucial component in advanced ceramic applications.
- Other Additives for Specific Properties
- Various additives can be incorporated into ceramic materials to enhance specific properties such as electrical conductivity, mechanical strength, or chemical resistance, tailored to meet the requirements of different industrial applications.
What is a fused silica ceramic brick?
A fused silica ceramic brick is a type of refractory material made from high-purity silica (SiO₂) that has been melted and then cooled to form a solid, non-crystalline structure. These bricks are known for their excellent thermal stability, low thermal expansion, and high resistance to thermal shock.
What are the primary applications of fused silica ceramic bricks?
Fused silica ceramic bricks are used in a variety of high-temperature applications, including: Glass furnaces Metallurgical furnaces Ceramic kilns Incinerators Other industrial processes requiring high thermal stability and resistance to thermal shock
What are the key properties of fused silica ceramic bricks?
High purity: Typically composed of more than 99% SiO₂. Low thermal expansion: Minimizes the risk of cracking due to temperature changes. Excellent thermal shock resistance: Can withstand rapid temperature changes without damage. High refractoriness: Capable of withstanding temperatures up to 1650°C (3002°F). Low thermal conductivity: Provides effective insulation in high-temperature environments.
How are fused silica ceramic bricks manufactured?
Melting high-purity silica: The silica is melted in an electric arc furnace or other high-temperature furnaces. Cooling: The molten silica is rapidly cooled to form a non-crystalline, glass-like structure. Shaping: The cooled silica is then molded into bricks or other desired shapes. Finishing: The bricks may undergo further processing, such as cutting or grinding, to achieve precise dimensions and surface finishes.
What are the advantages of using fused silica ceramic bricks?
Excellent thermal stability: Maintains structural integrity at high temperatures. High resistance to thermal shock: Can endure rapid temperature fluctuations without cracking. Low thermal expansion: Reduces the risk of expansion-related damage. High purity: Ensures minimal contamination in sensitive processes. Low thermal conductivity: Provides effective insulation, reducing heat loss.
Are there any limitations or drawbacks to using fused silica ceramic bricks?
Brittleness: The non-crystalline structure can make them more brittle compared to other refractory materials. Cost: High-purity silica and the manufacturing process can make these bricks more expensive than other types of refractories. Mechanical strength: May have lower mechanical strength compared to some other refractory materials.
How should fused silica ceramic bricks be installed and maintained?
Correct installation: Ensure bricks are properly aligned and secured to prevent movement and damage. Regular inspection: Periodically check for signs of wear, cracks, or damage. Timely repairs: Address any damage promptly to prevent further deterioration and maintain performance. Controlled heating and cooling: Avoid rapid temperature changes during initial heating and cooling to prevent thermal shock.
Can fused silica ceramic bricks be customized?
Yes, fused silica ceramic bricks can be customized to meet specific requirements. Customization options may include: Dimensions: Bricks can be cut or shaped to precise dimensions. Compositions: Additives or coatings can be applied to enhance specific properties. Shapes: Bricks can be molded into various shapes to fit unique applications.