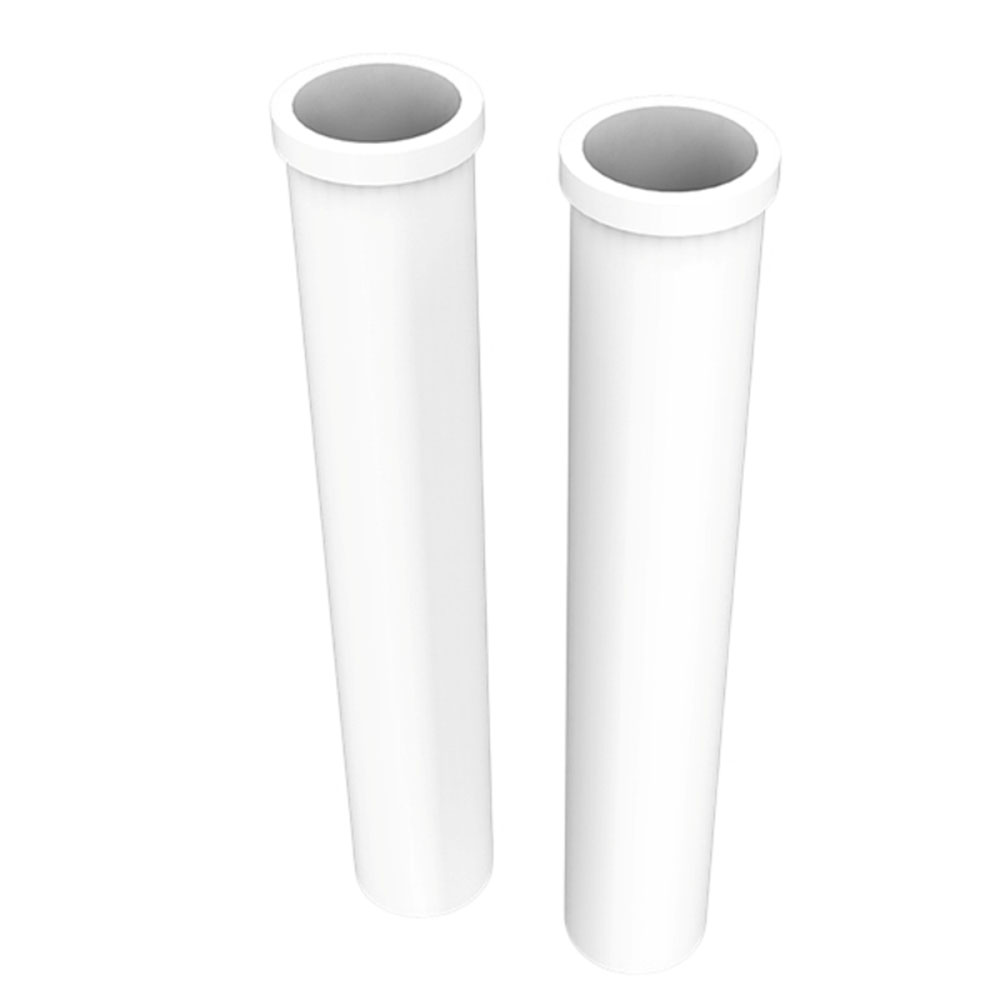
Fused Silica Barrels
✦ Excellent Heat Resistance: Made Of High-Purity Fused Quartz Material, It Can Withstand High Temperature Furnace Environment.
✦ Excellent Chemical Stability: Anti-Corrosion Properties, Suitable For Various Chemical Reagents And Solvents
✦ Precise Processing And Dimensional Stability: Precise Manufacturing Process, Precise And Stable Dimensions, Suitable For Precision Instrument Parts
✦High Transparency And Low Ripple: Excellent Optical Properties, Suitable For Laser Systems And Optical System Components
✦ Ultra-Low Thermal Expansion Coefficient: Extremely Low Thermal Expansion Performance, High Stability, Suitable For High-Precision Thermal Control Management
♦ Environmentally friendly and pollution-free: no harmful substances, green environmentally friendly materials, clean production process
Product Image
Fused Silica Barrels Certification
ISO9001,CE certification,RoHS environmental certification
Product specifications: Inner diameter: 20-150 mm, Length: 50-500 mm, Wall thickness: 2-10 mm
-
DESCRIPTION
-
SPECIFICATION
-
FQA
Fused Silica Barrels, also known as Fused Silica Rollers, are high-purity cylindrical components made from fused silica, primarily composed of silicon dioxide (SiO2). These barrels are engineered to offer exceptional performance in various industrial applications, particularly those requiring high-temperature resistance, chemical stability, and mechanical strength. With a purity level of ≥99.6%, Fused Barrels are ideal for processes that demand minimal contamination and superior material integrity.
Including fused silica plates, fused silica crucibles, material bowls for glass furnaces, ends, punch, stirring slurry, uniform cylinders, etc., widely used in vertical glass drawing pipelines and glass-ceramic production lines, also according to customer drawings products in other complex shapes. Due to quartz ceramics’ excellent thermal shock resistance, preheating the hot state is unnecessary; it is resistant to glass corrosion, has no pollution to the glass liquid, has high strength, and has a long service life.
Features of Fused Silica Barrel
✦ High Purity: Made from 99.99% pure silicon dioxide, fused silica barrels exhibit superior purity, ensuring no contamination in sensitive processes.
✦ Thermal Stability: These barrels can withstand extreme temperatures without deforming or degrading, making them ideal for high-temperature applications.
✦ Thermal Stability: These barrels can withstand extreme temperatures without deforming or degrading, making them ideal for high-temperature applications.Chemical Resistance: Fused silica is highly resistant to acids, bases, and other aggressive chemicals, ensuring longevity and reliability in harsh environments.
✦ Low Thermal Expansion: The minimal thermal expansion of fused silica prevents cracking and maintains structural integrity even under rapid temperature changes.
✦ Optical Clarity: Fused silica’s optical clarity allows for precise monitoring and measurement, crucial in applications like spectroscopy and photonics.
Applications of Fused Silica Barrels
Semiconductor Manufacturing: Used in the fabrication of semiconductor devices, fused barrels provide the high purity and thermal stability necessary for precision etching and deposition processes.
Aerospace and Defense: In these sectors, the exceptional thermal properties and durability of silica are vital for components exposed to extreme conditions.
Scientific Research: Laboratories use silica barrels in experiments that require high-temperature environments and resistance to chemical reactions.
Medical Devices: The biocompatibility and non-reactive nature of fused silica make it suitable for use in medical and dental instruments.
Optical Fiber Production: Fused silica barrels are integral in the manufacturing process of optical fibers, where their clarity and stability ensure high-quality output.
Our Fused Barrels are the perfect choice for industries that demand high performance, reliability, and durability. With their advanced material properties and precise engineering, they ensure optimal performance in the most challenging environments. Choose our Fused Silica Barrels for superior quality and unmatched performance.
Why Trust Kamroller
Kamroller stands at the forefront of fused silica technology, committed to delivering products that meet the highest standards of quality and performance. Here’s why you can trust Kamroller for your fused silica barrel needs:
Expertise and Innovation: With decades of experience in materials science, Kamroller continually innovates to provide state-of-the-art solutions tailored to industry requirements.
Expertise and Innovation: With decades of experience in materials science, Kamroller continually innovates to provide state-of-the-art solutions tailored to industry requirements.
Customer Focus: Kamroller prioritizes customer satisfaction, offering personalized service and technical support to meet your specific needs.
As a key material in the semiconductor industry and optical field, fused quartz barrels have important application value and development prospects. By optimizing the manufacturing process and improving product quality, we can better meet the needs of different fields and promote the development and innovation of related industries.
What are Fused Silica Barrels
Fused Silica Barrels: An important material used in the semiconductor industry with high purity and excellent heat resistance
What are the advantages of fused silica barrels?
- High temperature stability: Able to withstand extremely high temperatures without melting or deforming - Chemical inertness: Good corrosion resistance to a variety of chemicals - Optical transparency**: It has excellent optical transparency and is suitable for optical processing and detection. - Precision processing**: It can be precisely processed into various shapes to meet different needs.
What are the main application areas of fused silica barrels?
- Semiconductor manufacturing**: used to manufacture key components of semiconductor process equipment such as lithography machines and thin film deposition equipment. - Optical instruments**: suitable for manufacturing lenses and optical components of optical equipment such as telescopes and spectrometers. - Chemical experiments**: as storage containers for chemical reagents, they withstand high temperatures and corrosive substances.
What is the manufacturing process of fused silica barrels?
- Melting**: Heating high-purity silica material to a molten state. - Molding**: Molding the molten silica into a barrel shape using a mold or precision machining technology. - Annealing**: Eliminating internal stress by controlling temperature and time to improve the heat resistance and stability of the fused quartz barrel.
What are the common problems and solutions of fused quartz barrels? .
- Thermal shock cracks**: Cracks appear under rapid temperature changes. - Solution**: Optimize the annealing process to improve the thermal stability of the fused quartz barrel. - Chemical erosion**: Damage caused by corrosive substances such as strong acids and alkalis. - Solution**: Improve the surface coating or select materials with stronger corrosion resistance. - Shape inaccuracy**: Shape deviation or irregularity that occurs during the manufacturing process. - Solution**: Optimize the manufacturing process, strengthen quality control, and ensure product accuracy. - Internal bubbles**: Gases present in the material are trapped in the barrel, affecting its service life and performance. - Solution**: Optimize the material purification process, reduce gas residues, and improve material quality.
What is the maintenance method of fused quartz barrel?
- Regular cleaning**: Use a special cleaning agent to clean the surface to remove sediment and dirt. - Avoid collision**: Handle with care and avoid collision with hard objects to prevent surface scratches or damage. - Proper storage**: Avoid long-term exposure to high temperature or humid environment, and choose a dry and ventilated storage location. - Regular inspection**: Regularly check the surface for cracks or damage, and repair or replace it in time