Šta je kvarcni prah
2024.06.02hqt
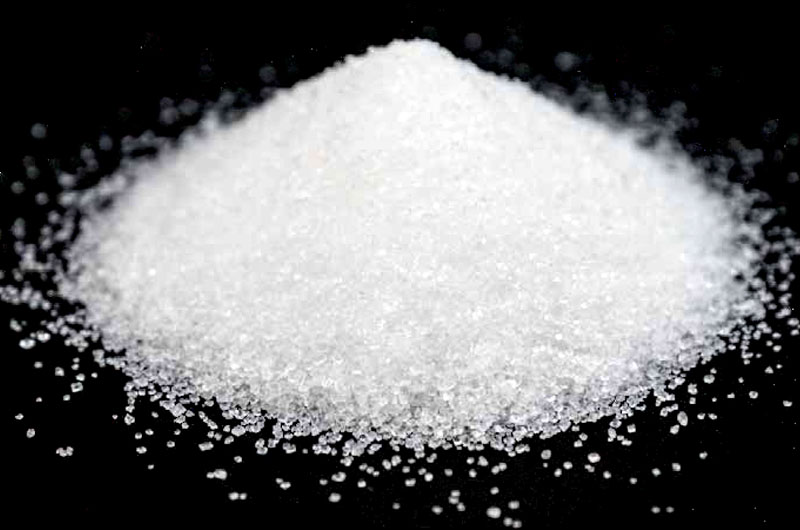
Kvarcni prah je praškasta tvar dobivena preradom i drobljenjem kvarcne rude. Kvarcni pijesak ili kvarcni kamen se mogu obraditi i mljeti kako bi se dobio kvarcni prah, koji je bijeli ili prozirni praškasti materijal sa širokim rasponom primjena. Zbog svojih jedinstvenih fizičkih i hemijskih svojstava, quartz powder is widely used in industries such as glass manufacturing, ceramics, coatings, casting, and electronics.
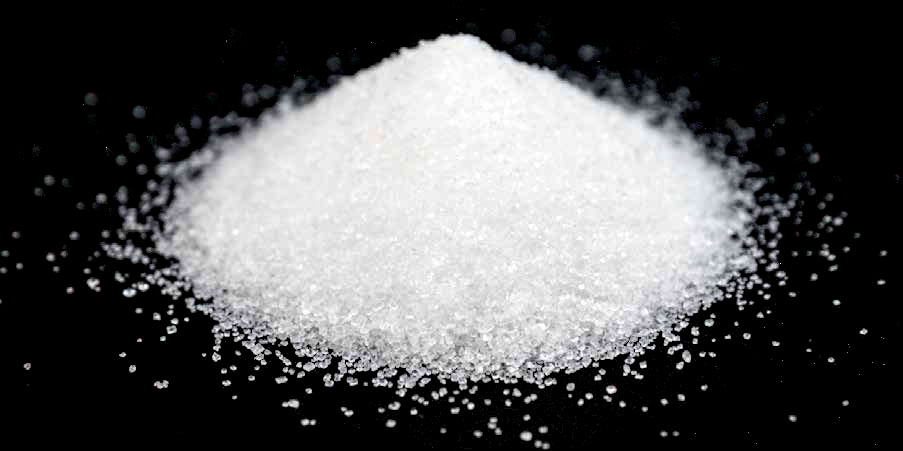
Composition of quartz powder:
The primary component of quartz powder is silicon dioxide (SiO2), which is a highly common compound. Additionally, quartz powder may contain trace elements such as mercury, lead, chromium, nickel, etc. Therefore, special attention to safety is required when using it.
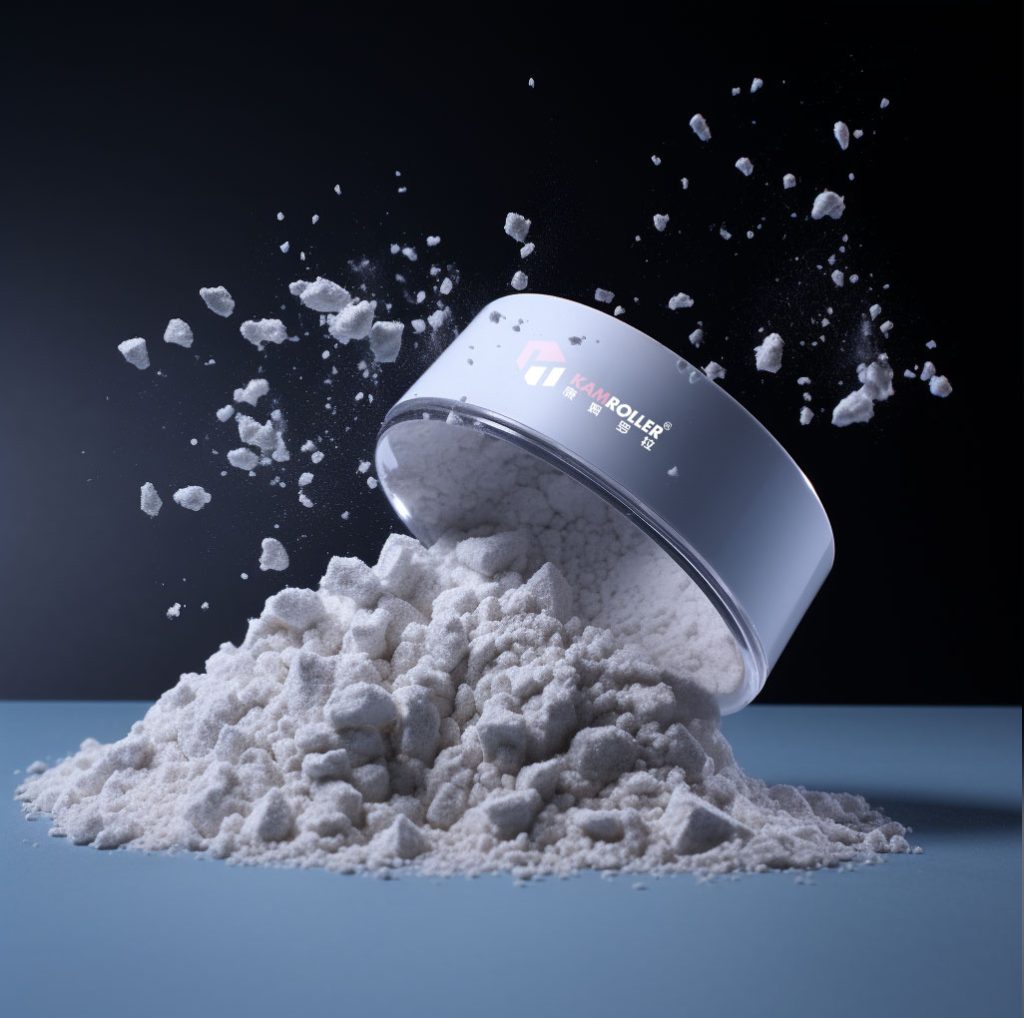
Uses of Quartz Powder
- Construction Materials: Quartz powder, when mixed with other materials, can be used to produce high-strength concrete with excellent performance.
In the construction materials sector, quartz powder finds extensive application. Apart from being utilized in manufacturing high-strength concrete, it is also commonly employed as a filler or additive to enhance the workability and ultimate physical properties of concrete. Quartz powder is further utilized in the production of quartz sand, which serves as filler in construction, road materials, and as a raw material in glass manufacturing. Due to its hardness and abrasion resistance, quartz powder is also used as a component in flooring materials, such as quartzite flooring.
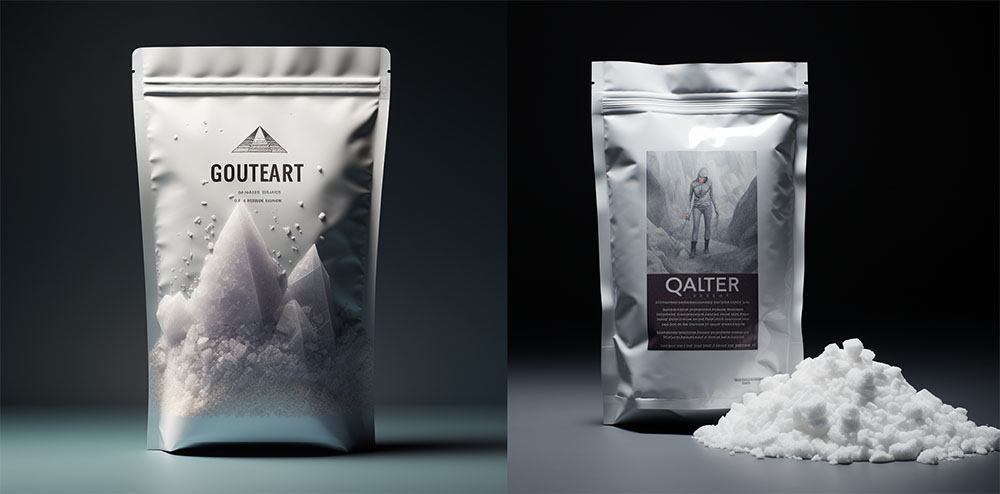
The Broad Application of Quartz Powder in Cosmetics
Quartz powder, a natural mineral, is widely used in cosmetics, primarily serving as a filler and thickening agent. It provides cosmetics with a smooth texture, enhancing the user experience.
Role as a Filler
As a filler, quartz powder effectively fills in the gaps in cosmetics, resulting in a more uniform and refined texture. This not only improves the appearance of the product but also enhances its adhesion, making the makeup last longer.
Role as a Thickening Agent
As a thickening agent, quartz powder increases the viscosity of cosmetics, making them easier to apply and spread. This ensures that the product glides smoothly during application without clumping or streaking, thereby improving the overall feel of the cosmetics.
Enhancing Texture and Performance
The application of quartz powder can give cosmetics a smooth texture, which is particularly important for base products like foundations and powders. The smooth texture not only makes the product easier to spread but also gives the skin a smoother and more natural appearance. Additionally, quartz powder can help absorb excess oil, maintaining the longevity and freshness of the makeup.
Application of Quartz Powder in the Electronics Industry
Quartz powder is a critical material in the electronics industry, where it is used to manufacture various electronic components such as transistors and integrated circuits.
Manufacturing Transistors
Quartz powder can be processed to create high-purity silicon, which is a fundamental material for making transistors. These transistors are essential components in numerous electronic devices, including computers, smartphones, and various digital appliances. The high-purity silicon derived from quartz powder ensures the transistors’ efficiency and reliability.
Creating Integrated Circuits
In addition to transistors, quartz powder is also used in the production of integrated circuits (ICs). These ICs are the building blocks of modern electronic devices, incorporating multiple electronic components into a single chip. The use of high-quality quartz powder in this process contributes to the overall performance and durability of the integrated circuits.
Enhancing Electronic Components
Quartz powder’s unique properties, such as its high thermal stability and electrical insulation capabilities, make it an ideal material for enhancing various electronic components. By using quartz powder, manufacturers can
Quartz Powder in the Ceramics Industry
Quartz powder is extensively used in the ceramics industry for the production of various ceramic products. Its excellent refractory and corrosion-resistant properties make it an ideal material for this purpose.
Creating Ceramic Products
Quartz powder is a key ingredient in the manufacture of a wide range of ceramic items, including tiles, sanitary ware, and tableware. Its high melting point and stability under high temperatures ensure that ceramic products are durable and can withstand extreme conditions without degrading.
Refractory Properties
The refractory properties of quartz powder make it especially valuable in the production of ceramic products that need to endure high temperatures, such as kiln linings and crucibles. These properties ensure that the ceramic items maintain their structural integrity and performance even when exposed to intense heat.
Corrosion Resistance
Quartz powder also imparts excellent corrosion resistance to ceramic products. This quality is crucial for items that come into contact with chemicals or are used in harsh environments. The resistance to corrosion extends the lifespan of the ceramic products, making them more reliable and cost-effective over time.
Quartz Powder in the Glass Industry
Quartz powder is a crucial raw material in the glass industry, where it significantly enhances the properties of glass products.
Improving Glass Strength
Incorporating quartz powder into the glass manufacturing process increases the strength of the final product. This added strength is vital for applications where durability is a priority, such as in construction, automotive, and various industrial uses. Stronger glass products are less prone to breaking, thereby enhancing safety and longevity.
Enhancing Glass Transparency
Quartz powder also plays a vital role in improving the transparency of glass. The high purity and consistent particle size of quartz powder allow for the production of clear and high-quality glass. This enhanced transparency is essential for applications like optical lenses, windows, and display screens, where clarity is paramount.
In summary, quartz powder’s unique properties make it an indispensable material in both the ceramics and glass industries, contributing to the production of high-quality, durable, and reliable products.
Preparation method of quartz powder
Methods of Preparing Quartz Powder
1. Physical Methods
One of the most common methods for obtaining quartz powder is through physical processes, including grinding and screening of quartz ore.
- Grinding: Quartz ore is crushed and ground into fine particles using various grinding equipment such as ball mills and vertical mills. This process reduces the ore to a powdery form.
- Screening: The ground quartz powder is then passed through screens to obtain particles of the desired size. This step ensures uniformity in the particle size of the final product.
2. Chemical Methods
Quartz powder can also be produced through chemical reactions involving silicates.
- Silicate Reaction: Silicates, such as sodium silicate or potassium silicate, undergo chemical reactions to form silicon dioxide (quartz powder). This method typically involves dissolving silicate in water and then precipitating silica from the solution.
- Purification: The resulting silica is then purified to remove any impurities, yielding high-quality quartz powder suitable for various industrial applications.
3. High-Temperature Methods
Another effective way to produce high-purity quartz powder is by heating quartz ore to high temperatures.
- Heating: Quartz ore is subjected to extremely high temperatures, which causes it to break down and release impurities. This process often takes place in a furnace or kiln.
- Cooling and Grinding: After heating, the quartz is cooled and then ground into a fine powder. The high-temperature process ensures that the resulting quartz powder is of high purity, making it ideal for applications requiring superior quality.