Choosing the Right Glass Tempering Rollers
2024.07.04администратор
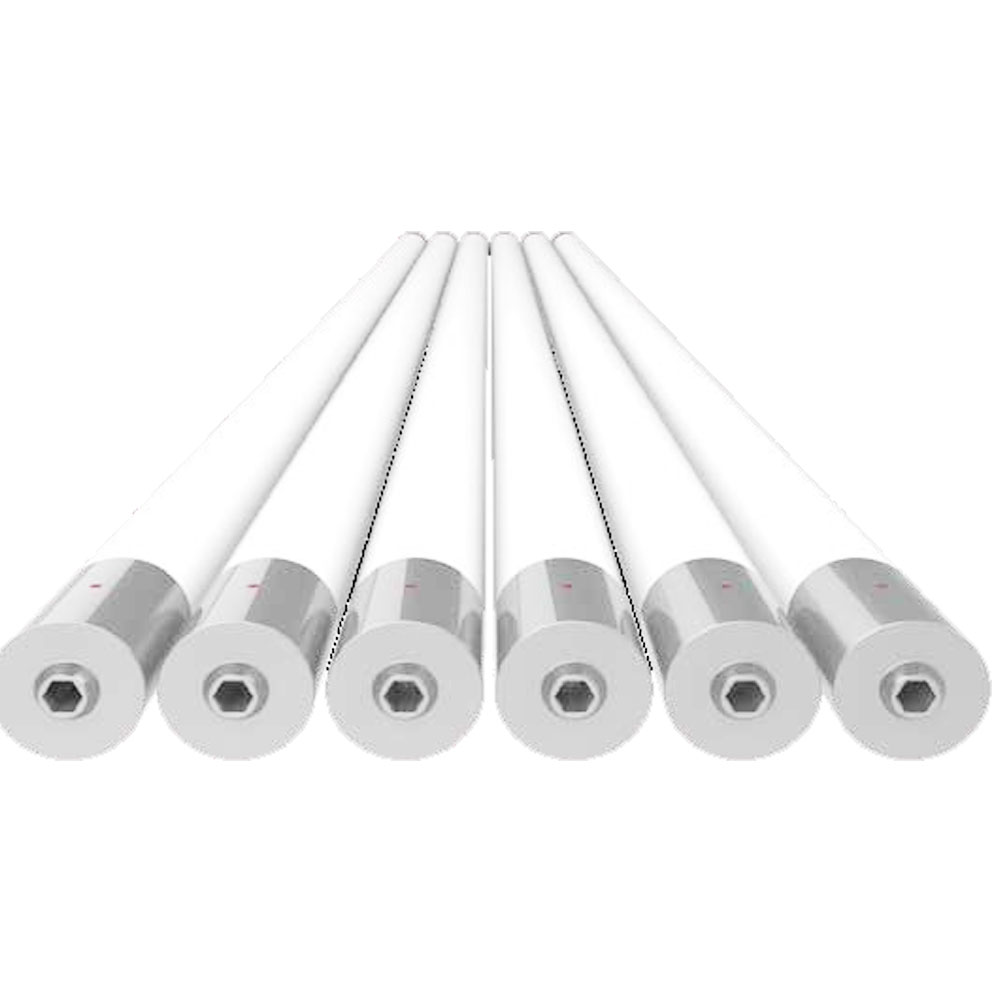
Glass Tempering Roller Introduction:
The rollers of the glass tempering furnace can be described as the heart of the above-mentioned equipment. These which at first seem like simple elements are vital in the production of high quality tempered glass which is used in many fields. This paper seeks to provide information on the types of glass tempering rollers and their uses in addition to outlining how the former contributes to the optimization of the furnace.
For the accurate engineering in the world, Fused Silica Roller for Glass Tempering Furnace is introduced to fulfill the requirements of glass tempering procedures. In the market of glass processing there is a new product called Fused Silica Roller for glass tempering furnaces – the tool is new and effective in its work.
Understanding the Glass Tempering Process:
Before defining what rollers are and how they work, there is a need to develop a foundation for glass tempering. To expand the types and possibilities of flat glass sheets it is heat tempered. In this process, the glass is heated to a desired temperature of about 600 degrees centigrade and then quickly cooled by air blowers. Therefore, when the quenched glass is compared with the untreated glass, the findings reveal that rapid cooling applies a compressive stress on the surface of the glass and thus enhance its already high resistance to cracking. In this operation, the glass sheets are transferred with the help of certain designed rollers while they are at the tempering furnace. These rollers serve several vital purposes:
- Supporting the Glass:
Hence, in both the heating and the cooling process, they still make sure that the glass sheets are kept flat and are still properly supported.
- Heat Transfer:
For an even heating of the glasses, rollers help in heating all the surfaces of the glass in an equal manner.
- Glass Conveyance:
At a controlled speed, the rollers assist in the movement of the glass sheet through various zones of the furnace.
Glass tempering rollers: A closer look:
The rollers are a lowlight team who are located in a rather provocative setting of a glass tempering furnace. Each of them is rather elementary; however, they are the key elements that help to create superior glass with improved properties. Nonetheless, rollers that are being sold in the market are not of the same standard. Let’s examine the several kinds frequently utilized for glass tempering rollers:
- Ролки от стопен силициев диоксид:
Fused silica rollers on the other hand are thermal stable and can withstand up to 1100 degrees centigrade of heat. These are suitable for rugged use because they feature a pristine glass look and only a very low level of resistance that arises from the product’s glossy finish.
- Ceramic Rollers:
Ceramic rollers have great wear and tear properties as well as the ability to withstand high temperatures of up to 800 degree centigrade; it is widely used in tempering furnaces. It allows the provision of heat in an efficient way since it facilitates tempering in an even way.
- Quartz rollers:
Fused silica rollers however, have their counterparts in quartz which have nearly the same thermal and dimensional stabilities. Въпреки това, it may be noted that they may be restricted in their use over fused silica primarily due to the phenomenon of devitrification which means crystallization at very high temperatures.
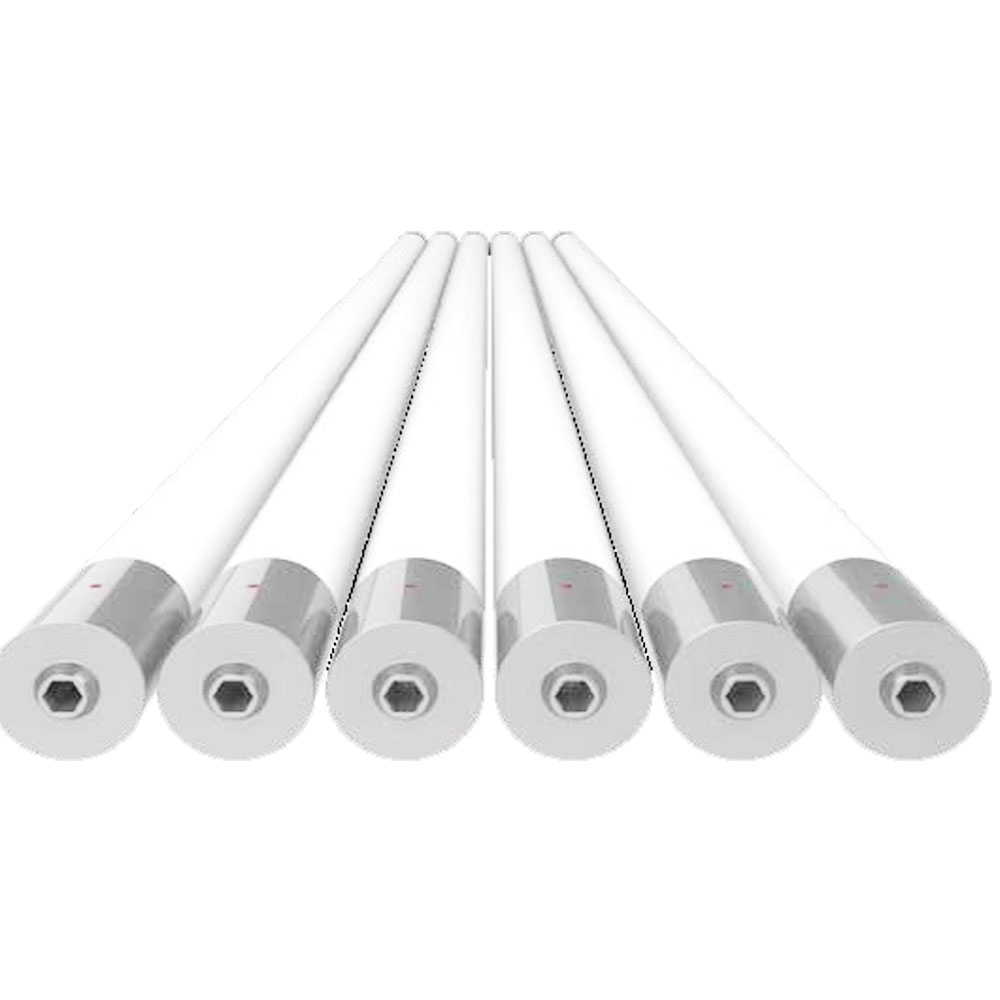
Hidden Factors in Glass Tempering Rollers:
Така, when choosing the right tempering roller the choice of the right material may be the easy part of the process. Several factors that are not very conspicuous end up having a very strong influence on your performance and hence the quality of your tempered glass. Here, we make these important points clear:
- Surface Finish:
To refer to the typical roller surface as your glass’s canvas. Its aesthetic should be very refined and possess a glossy surface. Small imperfections might just scrape or nick the glass sheet and thus damage the tempered layer, making it not very appealing to the eyes.
- Dimensional Accuracy:
Dexterity is essential. Uneven diameter of rollers could lead to improper or even spread of glass sheets all across the furnace. An uneven tempering might be caused, and the strength and possibly the safety of the finished product affected by this altering of heat distribution.
- Capacity to Load:
Superpose a bridge that many cars pass through. Similarly, glass tempering rollers must have sufficient stiffness to carry the weight of the sheets of glass without sagging or distorting. Low load essentially may lead to rollers wearing out a situation that may have an implication on the flatness of the glass and cracking of the same.
Performance Enhancement
These further elements can improve your choice of rollers even more:
- Thermal Conductivity:
Така, the concept of tempering relations on uniformity relies on efficient heat transfer. It is advisable to use ceramic rollers or any rollers that have high thermal conductivity to ensure that the heat is properly uniformly distributed across the surface of the glass sheet.
- Wear Resistance:
Conditions within a furnace could be harsh. Nobody wants a roller on their machine that gradually wears off shape and function, therefore, by picking rollers with excellent wear resistance like certain ceramic and fused silica models one is sure of getting high-quality rollers that will not wear out in the middle of the enterprise.
The unspoken matters can also be considered in choosing the best glass tempering rollers apart from selecting the best materials. Remember that proper rollers provide optimal operations of a furnace, minimize wastage, and in the long run help in making a better quality of the finished product that is the tempering of the glass.
How to Maintain Your Glass Tempering Rollers?
To give off their best performance, these tempering rollers just like any other good member need to be taken for maintenance. Here’s how to make sure your furnace keeps generating high-quality tempered glass and your rollers stay happy:
- Regular Cleaning:
It is advisable to clean the roller surface more frequently depending on the number of prints that have been made so as to remove any debris, dust, or any remnant of the glass. This helps to avoid them interfering with heat transfer and probably creating a scratch on the glass. While using a vacuum cleaner to clean loose debris, to remove tenacious dirt, a moist cloth that has been dampened with distilled water or anhydrous alcohol should be used. Remember to avoid materials that would compromise the roller surface health for instance abrasive chemicals.
- Vigilance is Key:
Take routine checkups and work like a detective to locate issues. Also, ensure that the upper surface of the roller is not damaged like it has chipped or cracked in some areas. When the rollers used in the production and tempering of the glass are damaged then the quality as well as the safety of the final product, which is the tempered glass, may be at risk. Since the breakdowns are identified in the early stage, there is reduced time taken to replace the faulty part hence maintaining a steady production.
Finding a Reliable Glass Tempering Roller Supplier:
It therefore becomes clear that the rollers are a vital commodity in the glass tempering furnace team. But who can you turn to find a provider that ensures this unsung work at its optimum? Here’s how to pick a winner:
- Experience Counts:
Ensure that the provider comprehensively understands rollers and corresponding types of glass and tempering methods. According to your specifications, they have to inform the optimal solution regarding the kinds of applications, for example, wear reduction, and high-temperature resistance.
- Dependable Quality:
When it comes to quality, dependability is a must. Choose a provider that has its quality control in check to guarantee the achievement of the proper roller dimension and finishing of surface polish and load limit. Certifications and traceability documents enhance trust as part of the continuous corporate social communication.
- Beyond Products:
Try to find an advocate that delivers more advantages. Purchasing options for customized furnaces ensures that they meet the unique requirements of the special furnace. Technical help provides access to professional advice in terms of maintenance, selection of the replacement option, and problem-solving.
But if you make these factors as your priorities, you will find a reliable supplier that will be constantly your partner for your rollers and provide you the wonderful tempered glass. Remember that selecting the right supplier is one of the critical determinants of the success of any venture. Visit our website to explore our selection of high-quality glass tempering rollers.
Заключение:
At ГЪРБИЧНИ РОЛЕРИ it is known that to obtain the right glass tempering rollers section is something vital. To suit your application requirements, the following high-quality rollers, quartz, ceramics, and fused silica are available among others. Are you prepared for the improvement of tempered glass supply? Come to us today for a consultation on your needs and see how our rollers will be of advantage to you.
Also Read: Какво е кварцова керамика? Свойства, Приложения & Ползи